By Kent Griffith
June 7, 2022 | Graphite, humble layers of hexagonally arranged carbon, has been the anode material in commercial lithium-ion batteries for over thirty years. There are seemingly daily updates about alternative anodes such as silicon and lithium metal, but what is new in the world of graphite?
Battery-grade graphite falls into one of two classes: natural or synthetic. Natural graphite is mined while synthetic graphite is produced from petroleum feedstocks. Both materials are highly processed to yield a purified, milled, spheroidized, and coated product. Natural graphite has to be mined and concentrated while synthetic graphite must be graphitized at ca. 3,000 °C. The environmental footprint of graphite is thus highly dependent on the ore grade, processing efficiency, and energy source of the manufacturing facility.
Historically, nearly all of the battery-grade graphite has come out of China. The United States is 100% import reliant according to the U.S. Geological Survey. Vehicle electrification and the transition away from fossil fuels has shifted Western energy security policies toward domestication of lithium-ion batteries from raw material extraction all the way through processing to final cell manufacturing.
Mark Thompson from Talga opened the discussion on graphite at the 2022 International Battery Seminar by pointing out the misaligned timescales upstream in the battery supply chain, noting, “It takes three years to build a battery factory, it takes about ten years to build a mine. There is a huge disconnect between the supply of raw materials and desired volume of batteries.” Talga, headquartered in Perth, Australia, is developing natural graphite mines in northern Sweden. Their R&D headquarters are in Cambridge, United Kingdom.
Thompson thinks that graphite is relatively overlooked in the battery ecosystem in part simply because it is not a metal. However, he noted that the graphite anode is responsible for up to 50% of the CO2 emissions from battery production. Compared to synthetic graphite that is often processed with coal power in Mongolia, Thompson emphasized that “Earth metamorphizing carbon for you saves a lot of energy.”
Coming back to resource grade and scale, the two Talga projects in Sweden—Vittangi and Jalkunen—each contain 4.7 million tons of graphite at grades of 24% and 14.9% graphite, respectively. High graphite content in the ore translates to lower raw material that must be extracted from the ground. Ore grade is not the only relevant metric; overburden and barren rock (waste rock that must be removed to get to the ore deposit) as well as processing losses combine to determine the total volume of material that must be moved to reach the final product.
A recent study in Environmental Science and Technology calculated these factors together to determine the “rock-to-metal” ratio for the production of 25 mineral commodities (Figure 1). Unfortunately, values were not available for graphite, but the data provide context for battery-relevant minerals such as lithium, cobalt, nickel, iron, titanium, silicon, copper, and aluminum. According to Talga, process innovations in float recovery rate and anode-feed flake size suitability enable them to realize processing yields of 78% from ore to anode, which they estimate to be nearly four times higher than some leading competitors. So, while some data related primarily to waste rock is missing, it seems reasonable to put graphite in the lower right-hand corner of the rock-to-‘metal’ chart.
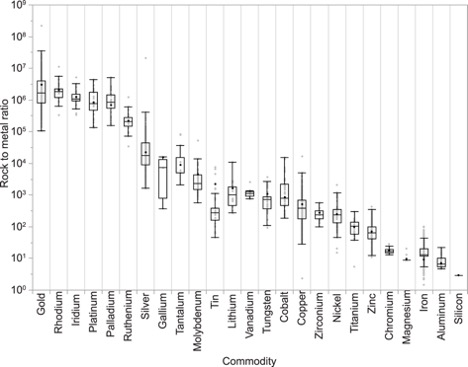
Talga estimates that their facility powered with renewable energy in northern Sweden can process enough graphite for 100 GWh of batteries with only 100 metric tons of CO2, compared to 3,700,000 metric tons of CO2 from a China-based synthetic graphite plant. Note that the energy demands are 2.3 TWh vs. 4.1 TWh, respectively, so the enormous difference is primarily in the carbon intensity of the energy source. Putting this together with the aforementioned resource considerations could translate to 2.9 metric tons of CO2 saved per 76 kWh electric vehicle battery (Figure 2), which represents a substantial fraction of the approximately 4–15 metric tons of CO2 required to produce a battery of that size.
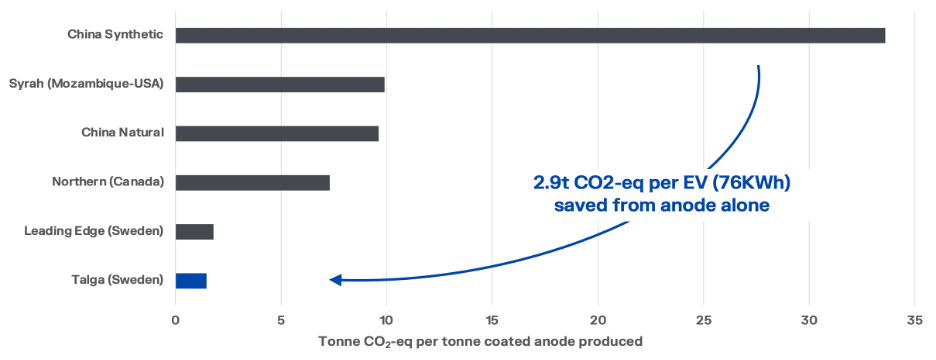
Graphite supply and demand mismatch was echoed by Bridget Deveney of Vianode, a Norwegian graphite producer. In terms of both cost and environmental impact, she highlighted a subtle point that the low bulk density of graphite (0.6 g/cm3) is unfavorable for shipping it from Asia to the booming class of European Gigafactories. With the high shipping container costs, what used to add $0.07–0.08/kg now adds $0.40/kg. Vianode will produce graphite with a low carbon footprint through the use of clean Norwegian hydropower and a closed furnace system that has better heat utilization and lower emissions than open furnaces.
Talga commissioned their first anodes in March 2022 with plans for 20,000 m.t./year in 2024 and an expansion to 100,000 m.t./year of their signature Talnode-C product in 2025–2026. Vianode is doing product scale-up in an industrial pilot plant with capacity of 200 metric tons per year. Though they started only a year ago, Vianode is an Elkem company, one of the largest producers of metallurgical silicon and an experienced material manufacturer. As a result, Vianode is scaling fast with plans for a 4,000 metric tons/year plant in Herøya, Norway in 2023 and a 70,000 metric tons/year plant in 2024. Their site sits on an island in the middle of a fjord. Both companies are also developing silicon–graphite composite anodes.
Looking to the North America, Anovion Battery Materials is building out a synthetic graphite supply chain with three plants planned in the southeastern U.S. A merger of Amsted Graphite Materials and Pyrotek, Anovion came onto the scene in March 2022 behind decades of experience in synthetic graphite manufacturing and graphite anode production. Jeremy Schrooten and Ian McCallum of Anovion shared their technology and future plans at the International Battery Seminar. By 2025 the company is targeting 30,000–50,000 tons/year, with a roadmap to 150,000 tons/year in the longer term. They hope to capitalize on graphite anode market growth that they predict to expand from 1,200,000 tons in 2021 to 6,900,000 tons in 2031. The presenters see the North American share of that market at 900,000 tons by 2031 with a 50:50 split of natural and synthetic graphite.
Novonix, another North American synthetic graphite manufacturer, brought a large team to exhibit at the conference Orlando. Last summer, Novonix purchased a second facility in Chattanooga, Tenn. that will allow them to expand their graphite production capacity to 10,000 metric tons/year by 2023. Their Chief Scientific Advisor, Jeff Dahn, stated in his plenary lecture that, “Natural graphite is not competitive with synthetic graphite for long lifetime cells.”
Graphite is a critical mineral not to be overlooked in the battery space. Supply is racing to keep up with demand, which means new mines and new synthetic production. While invested parties will debate the merits of natural vs. synthetic graphite, the reality is that the expansion of gigafactories for EV batteries will create a demand for any quality graphite coming online for the foreseeable future.