By Kent Griffith
February 7, 2022 | Silicon has a long history at the Advanced Automotive Battery Conference and—if the excitement of AABC 2021 was any indication—a bright future as well. The event was held in person in San Diego last month for the first time in two years, being simultaneously broadcast online and now available for asynchronous listening to all recorded live and virtual presentations. Many of the biggest names in silicon battery technology and several emerging players were there to give their outlook on this lithium-ion battery anode material with capacity for exceptional energy storage.
It is not difficult to see why there has been well over two decades of sustained interest in silicon as a lithium anode material. After oxygen, silicon is by far the most abundant element in the Earth’s crust, making raw silicon cheap and abundant. It can also store more lithium per unit mass or volume than any other element beyond lithium itself. While theoretical energy density is one thing, it is possible that, in practice, silicon can even surpass the energy density of pure lithium metal(!).
Let’s check that math. Based on the weight of the lithium-containing anode material, the charge storage is 3,862 mAh per gram of pure lithium, whereas silicon (as Li15Si4) holds 1,857 mAh per gram. Lithium thus wins in the case of a so-called “anodeless” battery with no excess lithium metal; however, silicon starts to take the edge if the cell is constructed with an actual lithium metal anode that exceeds the quantity of cyclable lithium. For a battery with 3–4 mAh/cm2 areal capacity, this corresponds to just 15–20 µm of lithium. There is thus little headroom for lithium metal over silicon, and the gap shrinks further when comparing the more relevant metric (for most applications)—volumetric energy density—because silicon and lithium-silicon alloys are considerably more dense than lithium, by a factor of two or more.
Folks like Jeff Dahn worked extensively on silicon and silicon/carbon materials in the 1990s. Numerous companies have spent a decade or more developing silicon anode technologies. Yet, despite much R&D, silicon has only found its way into battery anodes recently and, with a few small exceptions, as a minor (~5%) additive to graphite.
Challenges, Predictions
When it comes to silicon, the issues are well described as “chemomechanical” degradation mechanisms, referring to the fact that they are both chemical and structural in nature. As a primer, silicon is fundamentally different from the familiar commercial lithium-ion battery electrodes such as graphite, lithium titanate, lithium cobalt oxide, or lithium iron phosphate, which incorporate lithium via an intercalation mechanism. Intercalation does not require substantial changes in the electrode host atomic structure and is typically associated with volume changes on the order of 5–15%. Silicon, on the other hand, reacts with lithium via an alloying mechanism that involves complete atomic rearrangement and can lead to volume changes of more than 300%. Not only does the exceptional volume expansion and contraction lead to pulverization of the electrode (Figure 1), it also destroys the delicate solid-electrolyte interphase (SEI) layer that forms at particle boundaries. Commercial lithium-ion battery electrolytes—organic solvents with solubilized lithium salts—are unstable and thus susceptible to reaction with any anode material that has an electrochemical potential below about 1.0 V vs. Li+/Li, and this includes both graphite and silicon. Graphite is known to form a stable SEI layer, thanks in part to its relatively small volume changes during lithium insertion and extraction. If the SEI layer on silicon cannot be stabilized, fresh surfaces will be exposed, leading to continued passivation reactions and consumption of the precious electrolyte (Figure 2). In addition to resistive surface layers, electrolyte depletion can occur wherein the cell effectively dries out and impedes lithium transport.
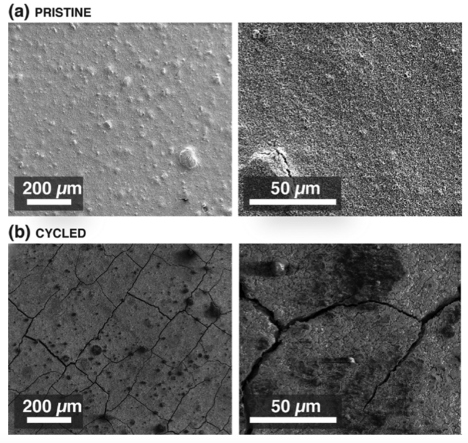
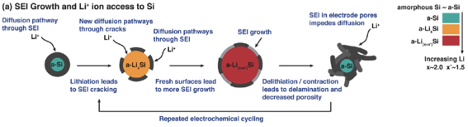
In order to realize silicon anodes in lithium-ion batteries, the chemomechanical particle and surface degradation mechanisms must be resolved. Already in 1999, Bourderau, Brousse, and Schleich noted, “[T]he modifying of the microstructure seems to be the key factor for the improvement of the cycle life of this kind of electrode.” Microstructure refers to properties such as the particle size, shape, and porosity, and encompasses nanometer-length scales that feature prominently in the world of silicon. Of course, nano/microstructuring is not without new challenges, primarily related to manufacturing cost and scale but also impacting the porosity and thus energy density of the resulting electrodes. Just as in the semiconductor field, low-grade silicon may be exceedingly cheap and abundant, but it is not generally suitable as a battery material. From AABC, it is clear that the routes toward overcoming these challenges vary considerably among the leading silicon material/battery companies.
Kurt Kelty, VP at Sila Nanotechnologies presented their silicon anode that can now be found in the Whoop 4.0 fitness tracker. According to Kelty, the Sila (pronounced “see-luh”) battery provides the Whoop with a 17% increase in energy density, enabling a 33% reduction in device size. Sila Nano spun out of Georgia Tech in 2011 and has since raised over $1 billion, submitted more than 100 patent filings, and worked through over “59,000 materials iterations”. They are targeting both mobile device and electric vehicle markets. Inside the battery, Kelty notes that Sila is cathode agnostic, and their anode material can be a 100% or partial replacement of graphite. He presented that their silicon anode has a capacity of 1500–1800 mAh/g (active material basis), first-cycle efficiency of 89–93%, can charge from 10 to 80% state-of-charge in 25 mins in a single-layer pouch cell, and has a typical cycle life of 800–1000 cycles. The Sila material is compatible with water-based slurries, an important manufacturing consideration with environmental and cost advantages over processing in organic solvents.
Another major silicon player is Enovix, a publicly traded company founded in 2007 and focused on the high-value consumer electronics market. Dr. Ashok Lahiri, CTO at Enovix, came to San Diego to discuss the company’s 100% active silicon anode, stating out of the gate that, “Silicon is the only material that cycles in our anode.” It is an exciting time for Enovix with production commencing this quarter. To achieve high energy density, Enovix takes a couple of different approaches. The first is a radically different internal design. Lahiri believes that prismatic cells are inefficiently packed, and so Enovix developed a horizontal stack of electrode strips wrapped on four sides with stainless steel and with a busbar through offset electrodes. This cell design enables their second innovation: rapid pre-lithiation across a short electrode distance to overcome first-cycle efficiency losses. The result? Enovix has built cells with silicon anodes and lithium cobalt oxide (LCO) cathodes that reach 900 Wh/l and 295 Wh/kg, measurements that Lahiri believes could reach 950 Wh/l and 320 Wh/kg with state-of-the-art nickel-rich cathodes.
Mentioned by virtually all presenters, first-cycle efficiency is an important metric for all batteries, but it is particularly problematic for silicon and even worse for silicon oxide. Because lithium is lost to SEI formation and parasitic side reactions on the first cycle, less lithium is then available to be cycled back and forth on subsequent charge and discharge steps. Pre-lithiation adds extra lithium to the cell to help account for these losses.
Group14 Technologies has a strategy moving toward silicon anode materials that evolved from their origins within a nanostructured-carbon company. Group14 spun out from EnerG2 in 2016 and has developed an anode product they call SCC55. According to their CTO, Rick Costantino, this powder comprises a carbon scaffold that has been impregnated with 2 nm amorphous silicon via chemical vapor infiltration. The company, based in Woodinville, WA, is not out to manufacture cells but to supply the anode material to customers who can incorporate it into their batteries as they see fit. Costantino remarked that their carbon-silicon composite is compatible with blends of 0 to 100% in graphite, in part because it maintains a 92% first-cycle efficiency that is high for silicon and on par with pure graphite electrodes. Group14 has already supplied materials to partners such as (i) Farasis for 82 Ah automotive cell benchmarking at 325–330 Wh/kg and 805 Wh/l for 1800 cycles and (ii) StoreDot for 0 to 80% state-of-charge fast charging in under ten minutes at 300 Wh/kg for 700 cycles. Strategic partners for Group14 include SK Materials, CABOT, ATL, BASF, and Showa Denko, and the first scaled battery-active material plant is set to come online this year in Korea followed by a US plant in 2023.
SiFAB—silicon fiber anode battery—has recently entered the lithium-ion battery space as a silicon play not from a start-up but from an established fiber material manufacturer. In breaking news, the acquisition of Lydall by Unifrax in 2021 has led to a new company called Alkegen that will be commercializing the SiFAB technology. According to company literature, their micron-sized silicon fiber anodes with a built-in nanoporous structure can achieve 1200 mAh/g, well over three times that of graphite, and can perform under fast charging conditions (4 C, 15 mins) and elevated temperatures (45 °C). Alkegen is developing a composite material with elemental silicon, silicon oxide (SiOx), and carbon. Designed to be highly tunable, the chemical and physical properties such as the material silicon/carbon composition and its porosity can be tailored to customer requirements. The product of well-established material manufacturers, SiFAB is moving quickly toward market with production lines expected this year.
Another relatively new entrant into the silicon ecosystem is Applied Materials, a company widely recognized in the semiconductor industry. Rather than elemental silicon, Applied Materials is focusing on silicon oxide (SiOx). Silicon oxide has some favorable properties but generally faces unacceptably low first-cycle efficiency, often 80% or less. James Cushing from Applied Materials shared the concept of leveraging their manufacturing expertise in the semiconductor and display industries to develop a scalable and efficient pre-lithiation process. Essentially, the idea is evaporation of a battery-grade lithium metal ingot and deposition onto the electrode surface. After wetting the cell with electrolyte, the pre-lithiation completes in just a few minutes, which is suitable for high-throughput manufacturing. Each production unit is expected to supply enough lithium for 1 GWh/year. Cushing believes that this technology could help meet the requirements for enhanced adoption of electric aerial vehicles.
One topic that was not widely discussed at the meeting was calendar life, a persistent challenge for silicon. In addition to cycle life—the number of times a cell can cycle lithium between its cathode and anode—calendar life is critical for commercial batteries because it describes the degradation that occurs when a cell is simply sitting on the shelf or in a device without being used. Calendar aging of silicon-containing batteries was recently covered in a scientific perspective article by an experienced team from many of the US national laboratories and several universities. A motivation for the perspective is that while the R&D efforts have led to cycle lifetimes approaching US Department of Energy targets, the evidence suggests that calendar life still faces a large technical gap. After the hard work on mitigating chemomechanical degradation during operation, let’s look forward to hearing about developments in calendar life for silicon-based batteries.
With widespread production scaling and market entrance coinciding with electrification across many sectors, the silicon space is full of action. Comprising 27.7% of the Earth’s crust, at least we know the question of elemental sustainability here is not an issue.