By Kent Griffith
March 14, 2022 | Solid-state electrolytes and lithium metal anodes often go hand in hand, but the road to the next generation of battery technology is branching and winding. An increasing number of cathode, electrolyte, and anode combinations are on the table, which raises some fundamental questions. Are liquid electrolytes compatible with lithium metal? Can solid-state electrolytes meet automotive battery requirements and manufacturing scales? Is lithium metal necessary for solid-state to get off the ground? The Advanced Automotive Battery Conference provided a platform for some of the leading lithium battery companies to share their thoughts and latest developments
Factorial Energy, Inc. was represented by Alex Yu, co-founder and president. Factorial came out of stealth mode last spring with a 40 Ah solid-state pouch cell, although their R&D started years earlier. The original company was Lionano, founded in October 2013, which then split into Lionano Inc. for cathodes and Lionano SE Inc. for solid-state batteries in August 2019. Factorial emerged in April 2021 as a rebrand from Lionano SE. Fundraising through Series D has seen investment from major automakers including Hyundai, Kia, Mercedes-Benz, and Stellantis. Factorial is now pursuing a parallel anode development strategy making battery cells by combining their polymer-based solid electrolyte separator with either graphite anodes or lithium metal anodes. The standard cathode of choice appears to be NMC811. At AABC, Factorial presented data showing a 40 Ah NMC811//graphite cell cycling for over 1,100 cycles with approximately 95% capacity retention (4.2 to 2.8 V; C/3–C/2 rate; 25 °C). At 60 °C, the same cell type under identical electrochemical conditions reached about 400 cycles before falling below 80% capacity retention and lasted 500 cycles before falling below 75% capacity retention, exceeding the performance of high-temperature cycling of NMC811//graphite cells with liquid electrolytes. Large-format (20 Ah) tests with NMC811/Li metal cells are still in the early stages (fewer than 200 cycles). Keep an eye out for those results at the next meeting.
In one indication of cell safety, nail penetration tests on 1.5–2.0 Ah NMC811//graphite and NMC811//lithium metal pouch cells with Factorial’s solid electrolyte reached maximum temperatures of 75 °C and 25 °C, respectively, compared to 260 °C for a NMC811//graphite cell with a conventional liquid electrolyte. Yu noted that Factorial’s core competence is in materials and cells and that they “do not want to compete directly with companies like LG Chem, CATL, SK [On]” but want to form partnerships to bring their product to the market.
Based on their data, QuantumScape is focused solely on lithium metal anodes, which are deposited on the first charge from lithium stored in the cathode. Thus, the QuantumScape cells are manufactured as so-called “anodeless” cells with a copper foil current collector and no lithium metal initially present. For the electrolyte, they use a solid ceramic separator with a small quantity of organic gel catholyte on the cathode side. Tim Holme, CTO, argued that regardless of cathode chemistry, a lithium metal anode is required to reach the desired energy density, and a solid-state separator is necessary to prevent dendrites. Those are certainly points of contention—ask any other company mentioned in this article. QuantumScape has set a commercial target of 800 cycles while retaining 80% of cell capacity, which roughly translates to 240,000 miles for a 300-mile battery pack. Their single-layer pouch cells significantly exceed this cycle life target, with internal testing and third-party testing performed by Mobile Power Solutions showing around 90% capacity retention at 800 cycles (>3 mAh/cm2; 25–30 °C; 1C/1C rate; no voltage range given; 3.4 atm applied pressure). A ten-layer cell under similar conditions retained about 85–90% capacity after 800 cycles.
A general outstanding question in the field of solid-state batteries is how much stack pressure is required and whether it is achievable in applications. Holme covered the history of the influence of pressure on solid-state lithium metal cells going back to 1983. He explained that pressure assists with minimizing overpotentials and flat metal deposition not only for lithium stripping and plating but also for other metals such as silver. Holme went on to provide examples showing that pressure is also beneficial in lithium metal cells with polymer electrolytes and even with liquid electrolytes (Figure 1). After his broad account of pressure effects, Holme leveraged the high-profile AABC event to release new data from QuantumScape showing cycling performance for the first time with zero applied pressure. In single-layer pouch cells similar to those described above, the zero-pressure cells retain 90% capacity after 400 cycles, with further testing continuing. These exciting preliminary results foreshadow increased design flexibility at the cell and pack level.
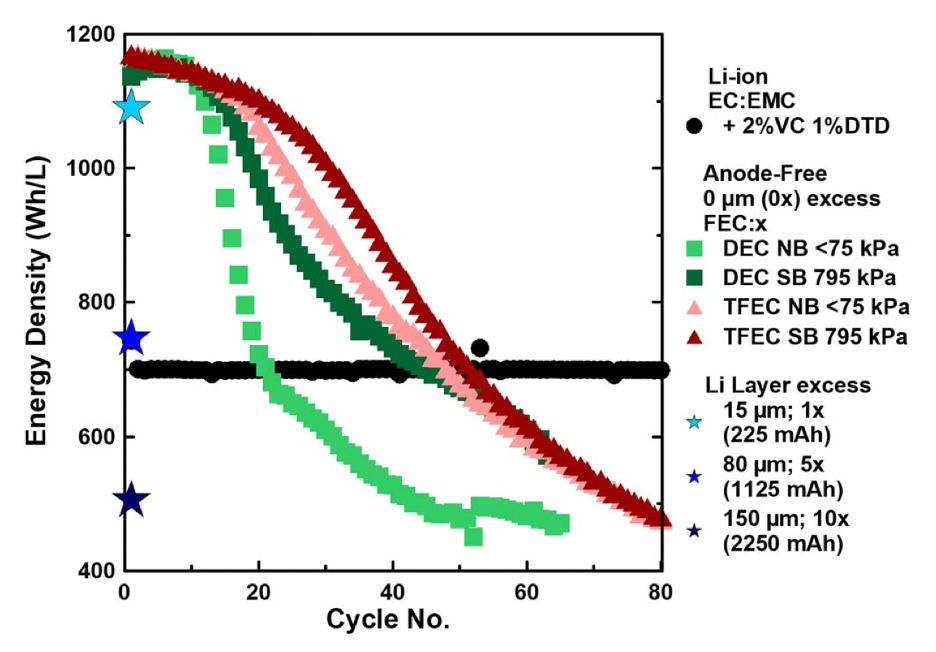
Solid Power is staying true to the concept of solid-state batteries. CTO Josh Buettner-Garrett emphasizes that they are one of the only companies building true all-solid-state batteries with no liquids, gels, or organic polymers in the electrolyte. Solid Power manufactures a sulfide solid electrolyte that they believe offers the ideal balance of mechanical and electrochemical properties.
The company, based north of Denver, CO, has a relatively broad approach to active electrode materials. They are working on lithium metal anodes while also developing alternatives that might be closer to market, such as silicon. At the moment, Solid Power is producing a little over 1 ton of sulfide solid electrolyte per year, but they have plans to scale to 6,000 tons per annum. A new 75,000-square-foot facility in Thornton, CO will help them achieve that goal. The electrolyte manufacturing plan also involves a strategy to shore up their supply chain, which is short on one key ingredient, lithium sulfide (Li2S). While they work on scaling up to 100-Ah cells for automotive qualification, Solid Power has released data on 20-Ah pouch cells that possess energy densities of 320 Wh/kg. Sulfide electrolytes could also help enable new cathode chemistries such as the ultracheap but electrochemically challenging conversion material iron sulfide (pyrite, FeS2). Solid Power showcased their all-solid-state cell performance under a variety of conditions. High-energy cells with silicon-based anodes and NMC cathodes can reach 750–1000+ cycles before falling below 80% capacity retention (3–4 mAh/cm2; 2.5–4.1 or 4.2 V; room temperature; 25–30 µm electrolyte thickness; up to 350 Wh/kg at stack level (excluding tabs and pouch)).
While the three examples above are all pursuing different solid electrolyte material families, other companies have chosen to target lithium metal anodes while forgoing solid electrolytes entirely. Both Sion Power and Cuberg (recently acquired by Northvolt) have chosen to employ proprietary liquid electrolytes to accompany lithium metal anodes in the quest for higher energy density batteries. Jeffrey Britt, COO of Sion Power, told the audience at AABC that the move from graphite to lithium metal anodes enables them to use half as much electrolyte thanks to the non-porous nature of lithium. Decreasing the electrolyte content not only saves expense but further increases the cell energy density. Britt reported that the state-of-the-art Sion Power product known as Licerion has been 3rd-party validated in a 17-Ah cell at 700 Wh/l volumetric energy density, 400 Wh/kg gravimetric energy density, and 800 cycles to 85% capacity retention. They are also working on cobalt-free prototype cells with lithium iron phosphate (LFP, LiFePO4) or lithium manganese iron phosphate (LMFP, LiMnxFe1–xPO4) cathodes. To protect their vapor-deposited lithium metal against reactions with the liquid electrolyte, Sion Power uses an engineered barrier coating. Richard Wang, founder and CEO of Cuberg, did not release many details about their lithium metal cells beyond that they use a non-flammable liquid electrolyte with industry-standard nickel-rich cathodes and polyolefin (referring to common polymers such as polypropylene and polyethylene) separators. He did report that Cuberg is more focused on the aviation industry than the automotive sector and that they are shipping multi-Ah prototype cells to prospective aviation customers
Oxide, sulfide, polymer, composite, all-solid-state, mostly solid with a dash of liquid or gel, all liquid—the industrially pursued options remain wide open for electrolytes for lithium metal batteries. The subset of solid-state batteries may be built with lithium metal anodes or even manufactured as “anodeless” cells that plate lithium metal the first time they are charged up. Alternatively, the emergence of solid-state batteries may not be synchronous with lithium metal at all, and the solid electrolyte may simply replace the flammable liquid in a cell containing cathode//anode pairings such as NMC//graphite or NMC//silicon.