Researchers at Purdue University are developing a method to mass-produce a new type of nanomaterial for advanced sensors and batteries, with an eye toward manufacturing in the Midwest. Research findings indicate the material shows promise as a sensor for detecting glucose in the saliva or tears and for “supercapacitors” that could make possible fast-charging, high-performance batteries. However, for the material to be commercialized researchers must find a way to mass-produce it at low cost.
“It’s one thing to say you’ve got a new wonder material, but can you prove that it can be made on a commercial scale?” said Arvind Raman, Robert V. Adams Professor of Mechanical Engineering. “In many cases we find that fundamental research needs to be done for scaling up. You want to be able to produce large quantities of the material at 50 cents per square meter.”
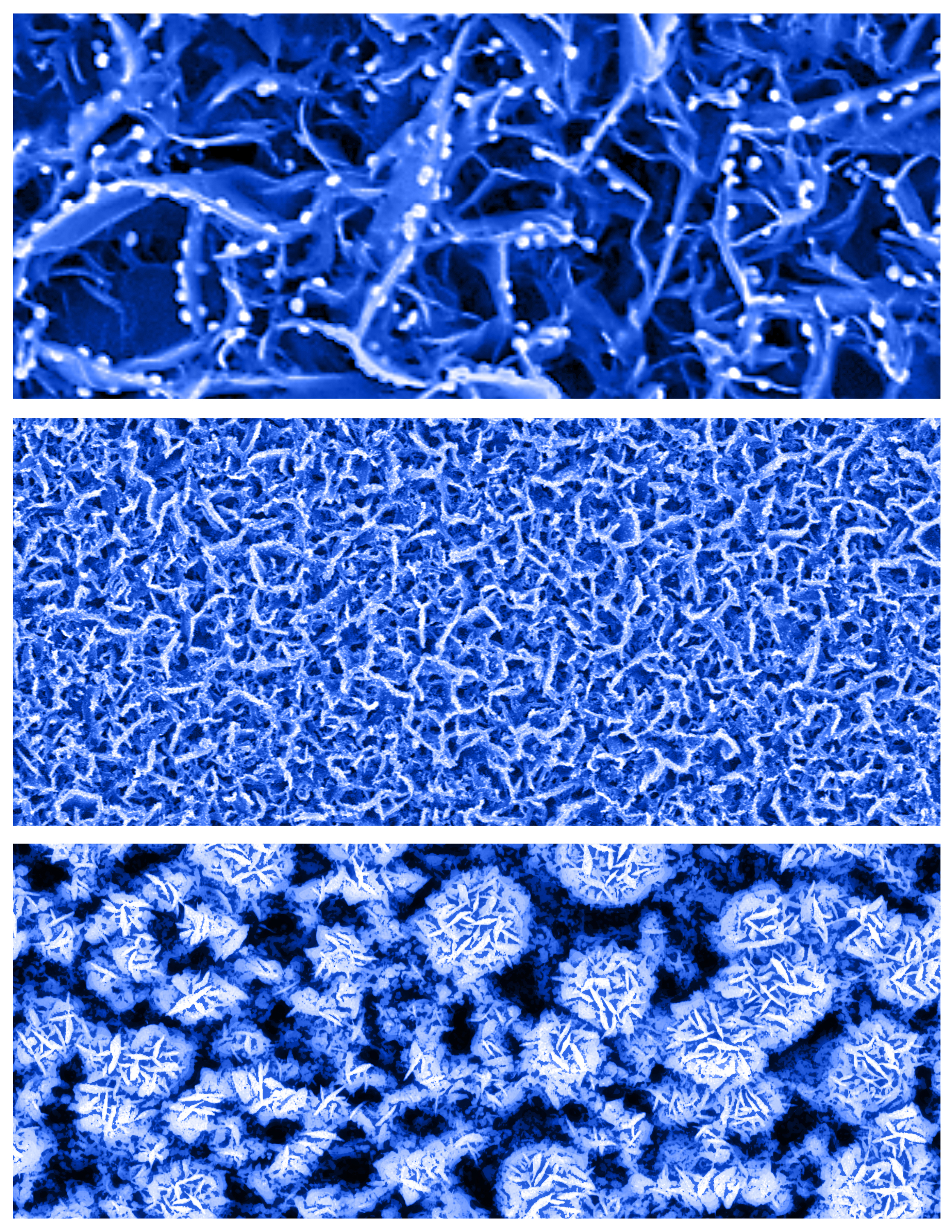
Now, a team of Purdue researchers will aim to do just that. The project, funded with a $1.5 million grant from the National Science Foundation, focuses on creating a nanomanufacturing method that is “scalable,” or capable of mass production at low cost.
The underlying technology was developed by a research group led by Timothy Fisher, the James G. Dwyer Professor in Mechanical Engineering. It consists of vertical nanostructures resembling tiny rose petals made of a material called graphene, which is a single-atom-thick film of carbon.
“Using these graphene nanopetals we have realized exceptional performance in a wide range of devices at laboratory scales,” Fisher said.
The researchers hope to boost the production speed of nanopetal-coated surfaces to 10 square meters per hour, representing a dramatic increase over the laboratory-scale production rate. Raman has expertise in roll-to-roll manufacturing, a mainstay of many industrial operations including paper and sheet-metal production. He models the mechanics of the process of creating flexible materials in sheets at high speed and under tension.
“A key factor is going to be industry partners,” he said. “There are many industries that have roll-to-roll operations. So focusing on roll-to-roll as a platform for doing nanomaterials production is very strategic for the Midwest.”
He also has expertise in precision measurement using an atomic force microscope.
“You have to be able to measure the material while it is being manufactured, and this is a challenge because of the nanometer scale of the petals,” he said.
The graphene nanopetals also have shown promise as a “thermal-interface” material to keep computer chips from overheating.
“A slew of new device and material concepts based on graphene nanopetals are emerging in applications as diverse as carbon fiber composites and new thermal-interface materials,” Raman said. “Commercial interest is extremely high for this recent carbon nanomaterial. ”
Other key researchers in the project are Alina Alexeenko, an associate professor of aeronautics and astronautics; Alexander Wei, a professor in the Department of Chemistry; Ernesto E. Marinero, a professor of engineering practice in the schools of Chemical Engineering and Materials Engineering; and Euiwon Bae, a research professor of mechanical engineering.
The nanopetals are created in a vacuum by exposing a cloth of carbon fiber to high-energy plasma that contains hydrogen ions and other ingredients, a process known as plasma-enhanced chemical vapor deposition. Alexeenko will lead work to model the plasma reactor and to optimize its conditions for fast and environmentally friendly conversion of raw materials, such as methane and hydrogen, into carbon nanopetals.
Wei will functionalize petals with metal nanoparticles and enzymes that recognize glucose or other target molecules for biosensing. Marinero will focus on reliability of devices made using the nanomaterial, and Bae will work to ensure proper petal size by analyzing patterns of light scattering from the material’s surface.
Most of the research will be based at the Birck Nanotechnology Center in Purdue’s Discovery Park.
“Scale-up production is a key challenge facing nanotechnology,” said Ali Shakouri, the Mary Jo and Robert L. Kirk Director of the Birck Nanotechnology Center and a professor of electrical and computer engineering. “This NSF project is part of a broader nanomanufacturing initiative at the Birck Nanotechnology Center where we focus on roll-to-roll production of smart thin films for applications in pharmacy and food packaging.”
Wei said, “The project represents the front edge of a much larger movement at Purdue to synergize core research expertise in science and engineering in a way that provides graduate students with opportunities to overcome the challenges of converting exciting research discoveries into products that can be commercialized.”
Technologies developed in the project might be commercialized through collaboration with a local start-up company, Folium Nanotechnologies LLC, co-founded by Fisher and Marinero, as well as Roche Diagnostics and the Battery Innovation Center. The center was launched this year to leverage Indiana’s public- and private-sector assets in advanced battery technologies to facilitate research and development, rapid prototyping and contract manufacturing for industry, academic and military customers.
“A regional workshop series on roll-to-roll nanomanufacturing will be organized to serve as a catalyst to innovation in the Midwest by bringing together interested small, medium and large enterprises together with original equipment manufacturers and university researchers,” Raman said.
The new technology could be of particular interest to battery makers in Indiana.
The researchers also will make available advanced simulation tools for vacuum-based roll-to-roll processes. The tools will be available to companies through the cyberinfrastructure of the manufacturing HUB and nanoHUB, an interactive website that makes available scientific simulations, seminars, interactive courses and other specialized nanotech-related materials.
“We will educate the US workforce through an innovative online class on nanomanufacturing offered as part of the nanoHUB U initative,” Raman said.
The research has potential for broad impact.
“Many results from this research are not just applicable to graphene nanopetal technology, but rather to a wide variety of nanomaterials manufactured in low-pressure and ambient roll-to-roll nanomanufacturing processes,” he said.