By Kent Griffith
October 4, 2022 | Leading automotive OEMs and solid-state battery companies gathered in Chicago at the recent Solid-State Battery Summit to discuss the promises and pitfalls of this burgeoning technology.
Solid electrolytes are the core differentiator of a solid-state battery versus a conventional lithium-ion battery. In an all-solid-state battery, there is no liquid present and ions must traverse the solid electrolyte to cross between the cathode and anode on charge and discharge. According to Zhe Li of General Motors, more than 760 organizations around the world have filed patents related to solid electrolytes. However, the challenge with solid electrolytes is really at the interfaces with the electrode materials where mechanical separation or chemical or electrochemical reactions may occur, leading to poor contact and high internal resistance.
There are plenty of explanations for the emphasis and investment in solid-state batteries. Most solid electrolytes are less sensitive to temperature than liquid electrolytes, so a solid-state battery could conceivably give an operating temperature range of –40 to +100 °C, according to Li. He also notes that the pack architecture could be simplified in a number of ways: a bipolar configuration would simplify stacking and eliminate redundant voltage sensing and a non-flammable electrolyte with a wide operating temperature range may reduce or eliminate the need for cooling. Ramin Rojaee from Stellantis added that they have modeling suggesting pack sizes that are 20% smaller and 25% lighter with solid-state batteries if lithium metal anodes are used.
Hansen Cheng from Mercedes-Benz expects conventional lithium-ion batteries to reach a plateau in energy density around 850 Wh/l, and that solid-state technology will be required to go beyond this target. Their testing indicates that oxygen evolution from the cathode on thermal runaway will still be the biggest safety issue and that testing of liquid lithium metal against sulfide solid electrolytes did not show much heat or reactivity. Enhanced safety with solid-state batteries could also enable cell-to-pack architectures that lead to increased energy density at the pack level. It is worth noting that all of these are prospective benefits and that there is much debate among battery and automotive experts on whether these advantages can be practically realized.
Automakers are aware of the technical hurdles. Most solid-state batteries are tested under high external pressure conditions to create better interfacial contact and to facilitate homogeneous metal plating and stripping. Cheng of Mercedes-Benz highlighted that the 20% change in cell thickness with lithium metal anodes is a problem because, from their side, it would probably be possible to apply high pressure or accommodate the swelling, but not both. Frederik Morgenstern from the BMW Group noted that the compression layer in a solid-state battery would have limits, e.g., polyurethane foam might achieve 1/3 to 2/3 compression; the additional volume from this layer would negate some of the electrode-level energy density benefits. Compression foams also must operate for long times and at elevated temperatures, so this is an example where advanced pack-level materials may also be required for solid-state batteries. He also commented that polymeric separators used in conventional lithium-ion batteries are approximately 12 µm thick, and it is well-understood that production of thin solid electrolytes in this range is non-trivial.
In order to use lithium metal anodes, one needs to use anodeless cells where the lithium comes solely from the cathode, or develop a cost-effective and scalable solution to mass produce thin lithium foils. Neither of these are fully solved problems, though Blue Solutions does claim to have IP and experience in manufacturing 20 µm lithium foil with up to 160 mm width that would be suitable for large-format lithium metal battery cells. Anodeless cells would be more cost-competitive but need ultrahigh coulombic (charge) efficiencies of more than 99.9%.
The greatest challenge for solid-state batteries may be more practical and financial than technical. Matt Denlinger from Ford Motor Company noted that solid-state batteries will need to differentiate themselves from conventional lithium-ion batteries in order to motivate changes to the existing production equipment. “Parity will not be compelling,” says Denlinger, and that means solid-state batteries must compete not with the batteries of today but perhaps those of 2030.
Morgenstern echoed the sentiment that performance requirements are a moving target, going on to say, “Cost comes first, energy density comes second,” and said that improved safety is not enough, so solid-state batteries need to differentiate themselves in terms of performance without sacrificing a hit in cost, at least once at scale.
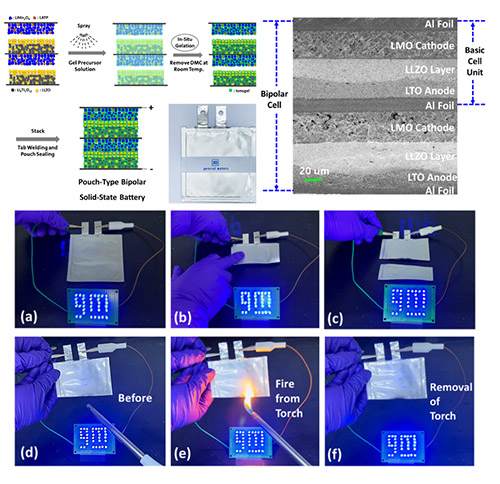
Partnerships are critical in the solid-state battery space, but exclusivity is not the model. OEMs are investing in multiple solid-state battery companies and solid-state battery companies are finding multiple OEM partners.
Auto companies are getting in the lab too. Mercedes-Benz announced that they are starting an in-house research program on solid electrolytes and solid-state batteries this year, and that they are agnostic to the solid electrolyte chemistry. According to Cheng, it may even be the case that multiple solid electrolytes are required to meet different energy, power, lifetime, and operating condition demands.
Research from General Motors has led to a new gel-based solid electrolyte that can serve as a soft medium to wet oxide–oxide interfaces, a notorious challenge that often forces oxide-based solid-state battery companies to add a small quantity of liquid at the cathode–electrolyte interface. The GM ionogel is a nonflammable composite containing a PVDF–HFP polymer solid matrix with solvent and a lithium ionic liquid. GM is also working on dry processing to make sulfide-based bipolar solid-state batteries. Dry processing requires less energy (and of course less organic solvent) than conventional slurry processing, and it has a further benefit with sulfide solid electrolytes because they are reactive with common solvents used in battery manufacturing.
The journey toward new and mainstream solid-state battery technologies for automotive applications continues (noting, as ever, that Blue Solutions has operated commercial vehicles with solid polymer electrolytes for many years).