Dan Friel, Director of Systems Engineering
Leyden Energy
Today’s consumers have never held more computing power in their pockets or purses. Mobile innovation is accelerating at an unprecedented rate as device manufacturers push the envelope of features and performance, as carriers race to keep pace with faster infrastructure, and as consumer demand grows for the newest capabilities in the sleekest packaging. However, at the heart of such a forward-thinking industry is a battery chemistry stuck in the last century, which has both consumers and mobile product manufacturers griping about battery life shortcomings, and is the only factor threatening to bring mobile device progress and advancement to a screeching halt.
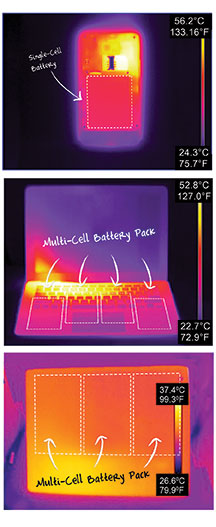
To meet the performance demand of mobile users, mobile processors are rapidly progressing ahead with vendor roadmaps, and 3D graphics capabilities are becoming an inherent part of the mobile experience, with bigger and brighter HD-capable organic light emitting diode (OLED) and liquid crystal display (LCD) screens to match. High-speed 4G LTE, WiFi wireless chips and high-capacity flash memory enable a high quality mobile experience through streaming, caching, download and storage of video, music and games. The entire mobile industry is moving at an ultra-fast pace to match consumers’ needs.
But while mobile semiconductors have indeed progressed in leaps and bounds, one key component has been left at the starting line: the lithium-ion (Li-Ion) battery. Although Li-polymer pouch cells are central to the design of ultrathin tablets, laptops and smartphones, these cells employ an electrolyte chemistry that comes with a host of issues, namely temperature sensitivity, which affect battery life, durability and safety.
In the last two decades, batteries have only roughly doubled their volumetric energy density, the amount of battery run time per charge a given volume can yield for the application. By contrast, within the same period of time, processor performance has improved more than a hundredfold. This improved performance is accompanied by higher running temperatures. The limitations of Li-Ion chemistry make batteries vulnerable to elevated temperatures, and this lack of thermal stability makes battery placement a major obstacle for device designers.
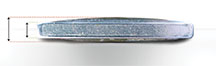
Increasingly powerful devices on faster networks require a deeper power source on which to draw, and traditional battery chemistries are not keeping pace. With every user that becomes frustrated with a device comes an opportunity to switch devices and perhaps carriers. How can the industry continue to accelerate, without hitting this roadblock? Next-generation mobile devices must be powered by a new generation of batteries that must be able to expand design possibilities for OEMs and offer increased durability and safety, allowing consumers to work and play efficiently.
Heat and the Death of the Li-Ion Battery
Most of today’s Li-Ion batteries in tablets, laptops and smartphones employ the same outdated, 20-year-old lithium hexafluorophosphate (LiPF6) electrolyte, which is the source of battery life, durability and safety issues, due to its vulnerability to elevated temperatures.
Temperature sensitivity, or lack of thermal stability, is precisely why Li-Ion cell datasheets generally show test results for cells and batteries at a “room temperature” of 20°C (68°F). However, what really matters is the in-device temperature. This is invariably much higher than room temperature, particularly in the context of today’s thinner, tighter enclosures that typically pack in far more heat-generating semiconductors than ever before, including multicore processors, high-speed wireless chipsets and high-frequency memory chips. That’s why the number of actual in-device charge/discharge cycles seems to come up short when compared to the advertised battery cycle life.
Heat Yields Rapid Decomposition
Today’s consumers live in a wireless age and expect the freedom to use their devices whenever, wherever. Consumers often leave their mobile devices in hot places, such as on sunny tabletops, in hot cars or pants pockets. Additionally, the in-device temperature is typically much higher.
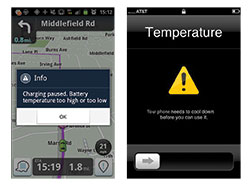
Unfortunately, the high temperatures from normal use cause decomposition of the LiPF6 electrolyte in the battery. Combined with residual moisture impurity within the cell, this can be problematic for the battery’s long-term health. Simply put, as temperatures rise, LiPF6 decomposes at a more rapid pace, generating hydrofluoric acid, an extremely corrosive substance. When the hydrofluoric acid reacts with the cathode in a cell, it begins to leach metal ions out of the cathode. These metal ions travel across the electrolyte and poison the anode, increasing cell impedance and bringing about the untimely death of the cell. Hydrofluoric acid can also cause swelling of the cell, which can damage the device and even pose a safety hazard.
Heat as a Design Roadblock
In an effort to inhibit degradation, designers attempt to place batteries away from the device’s hotter components; however, this restricts design and is quickly becoming impossible given increasing consumer demand for tighter and thinner devices.
Additionally, the temperature imbalance between one battery cell and the next can lead to an accelerated degradation of the entire battery pack in a multi-cell device such as a tablet or laptop. It does not matter that part of a battery pack is placed near a relatively cooler area of the device: if one section of the battery pack or a single cell within a multi-cell battery pack is in the vicinity of a hot point, such as where the tablet or laptop’s multicore processor is located, the entire battery will degrade at the rate of the fastest degrading cell. Additionally, the battery will suffer from accelerated performance degradation, and consumers may experience temperature-related software lock-ups.
Such lockups and other malfunctions become more likely when you consider the human factor, as mobile device designers must. What happens when the consumer leaves his or her phone or tablet in the car, in temperatures beyond 60°C (140°F), or when a laptop is placed on carpet or a duvet-covered bed, blocking its venting holes and leading to extremely hot in-device temperatures? What about the consumer carrying the smartphone in a pocket on their 37°C (98.6°F) person, or consumers who reside in more humid, less air-conditioned parts of the world? These are the consumers who come knocking on manufacturers’ service center doors for repair or replacement of their device, if not returning the device altogether and turning to another brand in hope of a remedy.
Heat and Safety Issues
Physical instability, manifested as swelling, is another issue plaguing Li-Ion cells that are packaged in a flexible pouch material to reduce overall thickness. Byproducts of cell corrosion (CO2 and CO gasses) can cause batteries to swell beyond the capacity of their cases, causing significant consumer safety risks. There are two mechanisms for swelling, both of which accelerate at higher temperatures.
First, the electrolyte tends to react with cathode and anode materials to generate a variety of gasses, a reaction that intensifies when the cell is fully charged. Thus, as the cell ages, it swells. In the dominant cell chemistry used today, the cell may increase in thickness as much as 10 to 12 percent by the time it reaches 80 percent of its original, rated capacity. To accommodate this, mobile device designers must leave more room for the battery in their device, which reduces the energy density (i.e., the effective run time available for a given volume) and makes it difficult to drive device thickness down, per consumer demand.
The second and more problematic mechanism is the reaction of the electrolyte with residual moisture in the cell, which generates hydrofluoric acid. In most circumstances, the hydrofluoric acid degrades the electrodes, forming a passivation layer and generating only minimal gas. However, if an auto-catalytic state is reached, gas production continues until the pouch cell swells or balloons to the point of bursting. The battery will then far exceed the allotted measurements of the cavity for which it was designed. This is one of the leading causes of battery recalls in consumer electronics with embedded batteries and a major headache for all parties involved.
New Batteries for the 21st Century
Given that more and more smartphones, tablets and laptops are now shipping with an embedded, non-removable battery design, the importance of having the right battery is clear. While it’s certainly easier to change an embedded battery in a mobile device than in a low earth orbit satellite, it still requires the consumer to either return the device to the store or ship it back to the manufacturer, which is a headache for support call centers as customers ask for return merchandise authorizations.
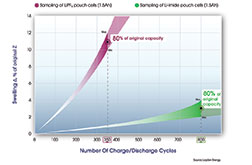
In addition, today’s consumers have become so attached to their mobile devices that parting with them due to a component failure often provokes negative online reviews and venting, thus hurting the device brand. Battery-related complaints account for a substantial number of online consumer reviews for some of the most popular mobile devices.
Tackling Thermal Instability
How can the industry overcome these battery limitations? First, customers require greater education on how to care for mobile devices. Apple’s website, for one, does very well in educating its customers about batteries and optimizing battery life.
However, education may not be sufficient when the underlying battery chemistry is flawed. Designers and manufacturers of mobile devices should consider alternative Li-Ion electrolyte chemistry platforms, such as the lithium-imide (Li-imide) electrolyte chemistry platform. Li-imide is durable and energy-dense, has longer cycle and calendar life and is far less susceptible to increased temperatures, thereby providing superior thermal stability and consumer safety. Additionally, Li-imide batteries do not need to be placed away from processors or other heat sources, and they require less cavity space to account for swelling, freeing designers from any restrictions caused by batteries.
The chart below compares a sampling of Li-imide pouch cells to a sampling of cells using the incumbent electrolyte, at a temperature of 40°C (104°F), per the mobile device norm. As is evident, the Li-imide cell is still delivering 80 percent of its rated capacity, and thus run time, after 800 cycles (more than 2.5 years of real calendar life if a consumer fully uses and recharges their battery everyday), and has only swelled 2 to 4 percent. By contrast, the sampled traditional cells lasted 350 cycles and swelled between 10 to 12 percent. The cost of this technology is on par with that of traditional Li-Ion technology.
What to Expect for Battery Life
To understand the full impact of temperature on battery life, mobile device designers need to ask some pointed questions of their battery vendors. They should separately consider cycle life and calendar life, which respectively translates to the number of charge/discharge cycles possible, and how long the battery maintains an acceptable run time per charge over its lifetime. Similar care should be taken with the battery’s physical stability. Elevated temperatures can also cause swelling, ballooning or bloating.
Most Li-polymer cell manufacturers today advertise between 300 and 500 charge/discharge cycles. This is one of the deciding factors in determining how long a mobile device’s battery can last through repeated charge/discharge cycles. First off, it’s important to note that cell manufacturers test cycle life at room temperature (20°C or 68°F) using accelerated methods that generate five or more cycles per day. A cell can reach 500 cycles in just over three months, which does not match the reality of longer-term consumer use.
But beyond that, factors such as depth-of-discharge (DOD) and temperature exposure have a major impact on battery life. First, as a mobile device designer, it is important to know whether these charge/discharge cycles are measured at 100 percent DOD or at a lower percentage, such as 80 percent. Not stressing the cell over its full range, and in particular, not fully charging the cell to its maximum voltage, at which cell degradation is accelerated, can generate misleading cycle life figures. For reference, reducing the cell’s DOD to five percent or less is how low earth orbit satellites achieve hundreds of thousands of cycles, as replacing a battery in a satellite is extremely difficult and costly. But this is not a practical solution in mobile devices, in which run time is critical. In a mobile device, if you decide to use only 80 percent of a battery’s full run time potential to increase cycle life, you will ultimately compromise the daily user experience.
Li-imide: Eliminating Battery Limitations
The new generations of faster processors in ever-thinner mobile devices are leaving Li-Ion battery technology behind. Li-Ion chemistry can’t handle the higher operating temperatures of today’s sleek, ultra-thin smart phones, tablets and ultrabooks. The result is compromised battery cycle and calendar life, consumer dissatisfaction with both device performance and battery life, and in some cases, damage to the mobile device or an actual safety hazard due to a swelling battery. Mobile device designers must operate under increasingly strict design limitations to mitigate these problems.
Li-imide batteries enable device designers to better satisfy customer demands and deliver a better overall user experience with higher performance in thinner mobile enclosures. They provide higher energy density per volume and weight, longer cycle and calendar life and increased thermal stability at wider temperature ranges. This both increases durability and prevents the ballooning of polymer pouch cells for increased safety. The battery can now last longer than the device.
Equally important is that mobile device engineers are now virtually free from battery-related design restrictions. Li-imide batteries need not be placed far away from processors or other heat-generating chipsets, and they require less cavity space to account for swelling.
For more information, please visit Leyden Energy at www.leydenenergy.com.