David White, Senior Member Technical Staff, Leon Adams, Sales/Marketing Manager, SouthWest Electronic Energy Group
Due to time and safety precautions built into vehicles, industry and consumers have grown comfortable with the safety risk associated with gasoline engines, even though gasoline presents a high energy safety risk. However, electric vehicles powered by Li-Ion battery packs are newer and not so well understood. This article will discuss the safety advancements that should be built into Li-Ion battery packs. It highlights battery management systems (BMS) to operate safe, efficient and reliable packs that prevent thermal runaway to make Li-Ion inherently safe for vehicles, bringing it into mainstream safe operation similar to gasoline powered vehicles.
What is Li-Ion Thermal Run Away?
Li-Ion thermal run away is a complex combination of chemical reactions and/or shorts inside the cell that are initiated by excessive heat from inside or outside the cell. It is not a classic electrical fire. The chemical reactions generate additional heat which causes a positive feedback cycle to intensify the heat until there are no reactive agents left within the cell.
What does Thermal Run Away Look Like?
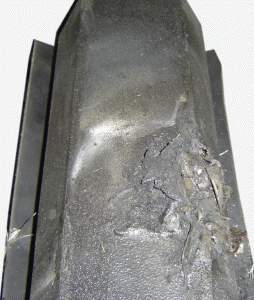
Thermal run away can look like smoldering or a fire with a flame. Figure 1 illustrates a moderate size battery pack after a single 2.2 Ah 18650 Li-Cobalt Oxide cell experienced thermal run away. Notice that the thermal run away reaction was vigorous enough to cause an eruption in the battery pack case. However, the battery pack construction, which utilized thermal heat spreading , prevented a chain reaction of other cells into thermal run away.
Different Li-Ion Cell Chemistry and Construction Can Reduce Thermal Run Away
Chemists and cell manufacturers have developed modifications to Li-Ion cell chemistries of the anode, cathode, electrolyte, separator and case to reduce the incidence and intensity of thermal run away. However, these changes come with some trade-offs such as lower cell capacity and/or higher cost.
For example, regarding the anode, exchanging Lithium-titanate for the carbon anode removes the passivation breakdown reactivity of the electrolyte with the anode, minimizing energy release, and reducing internally generated heat that facilitates thermal run away. The trade-off is cell capacity reduced to half or less of the standard Li-Cobalt oxide chemistry. Regarding the cathode, Lithium-iron phosphate offers significantly less reactivity compared to Lithium Cobalt oxide, thus it does not as easily decompose and release oxygen to source the internal burn of electrolyte if thermal run away approaches. However, it also causes a reduction to about half of the cell capacity of Li-Cobalt oxide chemistry.
Perhaps more promising is Nickel, Manganese and Cobalt oxide chemistries. Developed to reduce the expensive Cobalt content of the cathode, they reduce the reactivity of the cathode and limit thermal impact yet maintain the cell energy capacity equal to Li-Cobalt oxide, a seemingly preferred trade-off. In addition, changes to electrolyte, separator material, and case construction are all evolving to maximize safety and temperature range while attempting to maintain or increase cell Watt-hour capacity.
Li-Ion Battery System Design Can Reduce or Eliminate Thermal Run Away
There is no perfect cell chemistry with respect to performance and thermal run away trade-offs. Further, there is no one cell design that is functionally best for any or all power applications. Key to a safe and efficient Li-Ion battery is to conduct cell selection and battery system design with ample forethought of the target application in order to facilitate safety, performance and cost efficiency.
Selecting and Obtaining the Right Cell
First, select a safe cell chemistry and case construction that meets all customer and system design functional requirements. Perform in house or third party cell tests to verify that the cell meets battery system design requirements and assure that specs do not change without pre-approval. Qualify cell manufacturer(s) by confirming that a documented and verified quality system emphasizing continuous improvement is in place. Screen all incoming cells to verify continuing conformance to expected quality standards.
Physical Design of Pack and Module for Safety
To prevent thermal run away initiation, minimize retention of heat in the pack, including heat removal if required by high power activity. Prevent cell charging when cell temperature is below a cold temperature threshold (to avoid Lithium dendrite formation that can cause internal shorts) or above a high temperature threshold. The battery case should prevent damage from expected shock and vibration during transport and use, and minimize cell crush or penetration damage due to vehicle collisions. Provide for controlled release of excessive internal cell pressure in the battery case design. Use self extinguishing materials inside battery case. Consider installing a firewall between battery case and driver and passenger spaces. Fuse the battery to prevent electrical fire, spark, and shock hazard. Consider multiple insulation barrier(s) where high voltages are present.
Battery Management System (BMS) Design For Safety
Perhaps the most important aspect of the safe Li-Ion battery pack design is the BMS. Sometimes called the “pack protect circuit” or “safety circuits” in their earlier, less comprehensive instantiations, the BMS is the management brain of the pack that manages it within acceptable performance and safe operating conditions. These circuits have been improved over time to allow an almost unlimited number of series cell connections for high voltage, modular Li-Ion battery systems. Following are the typical safety requirements and capability of these systems.
• Cell Voltage Safety: The BMS should have a means to prevent any cell in the battery system from being charged or discharged if its cell voltage exceeds a safety threshold. High and low voltage safety thresholds should be set (lowered or raised) with respect to cell temperature.
• Cell Current Safety: The BMS should have a means to prevent excessive charge or discharge current through any cell in the battery system. Short circuit currents and extended length high current should be differentiated from expected high pulse currents (i.e., regenerative braking current). Fuses should be considered as a back-up to electronically controlled switches. If multiple cells are hard wired in parallel, fusible links should be considered to limit current flowing into a severely internally shorted cell.
• Cell Temperature Safety: The BMS should prevent charge and/or discharge current when the cell temperature is above a dangerous threshold to prevent initiation of thermal run away. The BMS should prevent charge current when the cell temperature is below a low temperature threshold to prevent the immediate creation of Lithium dendrites on the anode.
• Cell Balancing: Every non defective cell in the battery system should be balanced to the same relative capacity with the other non defective cells. If the battery system is constructed from series and parallel connected battery modules, a means to keep all the modules balanced is needed. If appropriate, a means to balance a recently replaced module with the other battery system modules should be provided. Balancing in all cases should be robust enough to keep up with expected sources of imbalance current.
• Charge Control: Thermal run away has been reported as happening more often when a cell is being charged, since charging stresses the cell both electrically (especially if cells are unbalanced) and mechanically (a Li-Ion cell expands slightly when charged). For this reason, internal autonomous charge control by the BMS is often a safety advantage over external charge control, providing automatic safety control by the battery for itself without depending on type of charger that may be used. As a minimum, if the BMS does not control the charge, feedback from the BMS should be provided to the external battery charger so it can be shut down by the BMS.
• Internal Short Detection: Internal Li-Ion cell shorts have been proposed by researchers as the primary reason for initiation of a thermal run away. Quality BMS designs have algorithms to directly detect both early onset and longer term wear-out aggregation of internal cell shorts and notify the vehicle operator to replace the defective battery/module. An option can be to automatically take action to discharge the battery/module to prevent or reduce the likelihood of a spontaneous thermal run away event.
• Safety Redundancy: Redundancy is a common in mission critical applications. It can be used by BMS and modular system design structure to improve battery system safety by shutting down dangerously defective sections of the battery system and then continuing operation at reduced capacity until replacement or repairs can be made.
In summary, Li-Ion battery packs can be a safe and reliable means of energy for electric vehicles by means of proper cell selection and pack design and manufacturing, including an advanced BMS to prevent thermal runaway. The BMS should adequately address cell voltage safety, cell current safety, cell temperature safety, cell balancing, pack charge control, cell internal short detection and module redundancy. Such functionality in a BMS enables Li-Ion battery packs to provide inherent safety control for vehicles and bring them into mainstream safe operation similar to or better than gasoline powered vehicles.
Leon Adams is the chief sales and marketing officer at SouthWest Electronic Energy Group. He has been in systems engineering, applications, marketing, and technical sales of battery powered embedded processing systems and battery solutions for over 20 years. David White is senior member of the technical staff at SouthWest Electronic Energy Group. He has been designing large, state-of-the-art electronic systems for 40 years.
For more information, please visit SouthWest Electronic Energy Group at www.swe.com.
This article was printed in the November/December 2011 issue of Battery Power magazine.