Michael A. Stout, Vice President Engineering
Falcon Electric, Inc.
Being in the UPS industry, Falcon Electric, Inc. is frequently asked why the industry hasn’t adopted the use of Lithium-ion (Li-Ion) batteries inside more products. Li-Ion batteries have a much higher energy density allowing them to be smaller and weigh less than half of an equivalent Valve Regulated Sealed Lead-Acid (VRLA) battery currently used in UPS systems.
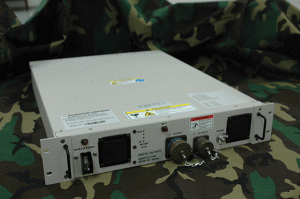
Li-Ion batteries (Figure 1) provide much longer on-battery runtimes and can be recharged faster than their VRLA counterparts. Unfortunately, high energy density Li-Ion battery packs have a number of issues that preclude them from being used in the typical commercial off-the-shelf UPSs. At the present time, with few exceptions, their use is limited to custom UPS products specifically designed for highly specialized applications.
With the large number of cell phones, computers and power tools now being sold with rechargeable Li-Ion batteries, it may seem a bit odd that their use inside a UPS would be a problem. The primary issues are cost, safety and federal regulations. Due to Li-Ion battery chemistries having differing levels of danger, the Department of Transportation (DOT) (in CFR 49, Sections 100 to 185) have divided the level of regulation based on primary and secondary battery types. Regulations are also based on levels of energy density. Other applicable regulations are United Nations UN3090 & UN3091.
A primary battery is defined as one that is shipped fully charged and cannot be recharged. Due to their chemistry and high level of charge available when shipped, Li-Ion batteries are considered the most dangerous. The crash of a freight carrier’s aircraft was recently suspected to be caused by a large number of lithium primary batteries that were onboard.
According to reports, the lithium primary batteries were not declared as hazardous materials. If lithium primary batteries become internally shorted, due to their high amount of stored energy and chemistry, they can generate enough heat to ignite the internal lithium. Once ignited, the remaining batteries in a shipping carton or on a pallet will ignite. The lithium fire would then burn at a high enough temperature to burn through an aircraft’s aluminum fuselage. Further, most standard fire extinguishers or aircraft fire systems are useless against a lithium fire due to its high burning temperature.
Secondary batteries have a differing chemistry and are defined as being rechargeable. They are usually shipped from their manufacturer partially charged in an attempt to keep the energy density as low as possible during transportation. The DOT and UN regulations divide secondary batteries into two basic categories, which are defined by the level of energy density contained inside the individual cells or batteries. The batteries used inside cell phones, computers and power tools typically fall into the lower energy density category and have much fewer transportation limitations; hence why they are allowed to fly on commercial airliners with passengers.
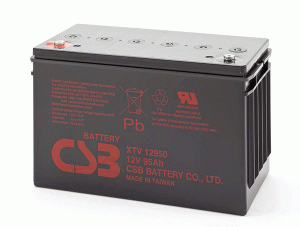
The batteries used in a typical UPS must be capable of supplying the high current demand of the UPS for a sustained period of time. The period of time may be from a few minutes to several hours, depending on the application. For many decades, the lead-acid battery (Figure 2) has met this demand. Its capability to supply the high current demands of the UPS is very good. However, its energy density to weight ratio leaves a lot to be desired. High power UPS systems capable of providing several hours of battery backup can have lead-acid battery banks weighing tons. The energy density of a lead-acid battery ranges from 30 to 50 Watt/Hours per Kg, while it is 110 to 160 Watt/Hours per Kg for Li-Ion chemistry batteries. This represents a weight reduction of two to three times that of an equivalent lead-acid battery. This makes Li-Ion batteries viable for use in electric vehicles as well as UPS products.
Unfortunately, all shipments of UPS units containing high energy density Li-Ion batteries, battery banks or batteries packaged inside a UPS must be shipped as class 9 hazardous materials and cannot be shipped on commercial airliners. They must ship by ground cargo only. This becomes very impractical and drives the costs associated with the incorporation of lithium batteries up even further.
There are substantial additional costs associated with the implementation of Li-Ion batteries in a UPS. First, there is the cost differential between lead-acid and Li-Ion batteries. Good quality Absorbed Glass Mat (AGM) VRLA batteries are very inexpensive and readily available. Their low cost is one of the reasons UPS manufacturers use them in their products. A typical 12 volt, 7 Ah VRLA battery designed to provide a five-year service life costs UPS manufacturers about $9.00. The same 12 volt Lithium-Phosphate battery costs more than $100, ten times the price. If a typical 6 kVA on-line UPS had a 240 VDC battery bus voltage, it would require 20 individual 12 VDC batteries to be installed. The cost to the manufacturer for lead-acid batteries maybe as low as $180, while the cost for equivalent Li-Ion batteries would be $2,000. This example is very conservative. A custom lithium-battery system for the same 6 kVA UPS might cost more than $10,000.
However, the cost of the Li-Ion batteries alone is not the total cost associated with proper implementation. In order to meet UN and DOT transportation regulations, one needs to incorporate adequate over-current protection and properly recharge the Li-Ion batteries. A specialized intelligent battery management system (BMS) must be incorporated into the UPS design. The BMS typically consists of a circuit board assembly or assemblies containing microprocessor battery monitoring, battery protection, recharge control and battery cell equalization circuits.
The primary function of the BMS is battery short circuit protection. Lithium cells have a very low cell resistance and a high energy storage capacity. A short circuited string of cells or batteries could be catastrophic and result in an explosion or very high temperature lithium fire. A typical BMS processor monitors the battery current and has a large semiconductor switch circuit that can be opened to prevent an excessive over-current condition. The second function of the BMS is to assure the proper recharging of the lithium cells. Cells can receive an initial high-rate charge current to reduce recharge time, followed by a long cell equalization charger to balance the cell voltages to within a few millivolts. The equalization charge is followed by the charge voltage being turned off to prevent cell overcharging and possible cell damage. The BMS also monitors to assure the charger voltage does not run away to the point of causing the cells to overheat and catch fire. The cost of the BMS board is substantial and has to be added to the cost of the Lithium-ion batteries and UPS. As the UPS market is very competitive, these added costs would price most UPS products out of most markets except military and specialized scientific applications. The cost of adding a BMS board to a UPS can range from $100 to more than $1,000.
To assure continuous protection of the batteries, the BMS must be powered and monitor the batteries continuously whether the UPS is turned on, turned off, during shipment and storage. This presents storage and non-use issues. Li-Ion batteries have a very low self-discharge rate. However, when the UPS is not being powered from utility power, the BMS must be powered from the batteries it is protecting. This accelerates the discharge rate, requiring the batteries be recharged far more frequently. With some BMS designs, recharging occurs every few months even while in storage. Like lead-acid batteries, should Li-Ion batteries be allowed to become too discharged, they can suffer internal damage, requiring their costly replacement. Their replacement can become even more costly due to the dangers associated with handling high-capacity Li-Ion batteries. They typically must be replaced by trained factory personnel, requiring the entire UPS to be returned to the manufacturer.
Federal regulations also dictate that all equipment containing high lithium content batteries be subjected to rigorous testing prior to any equipment being shipped. The test plan requires UPSs to be subjected to worst case tests. These tests are designed to assure the UPS has protections designed-in to protect the lithium batteries and assure proper safeguards are functioning to prevent a fire during transportation. A second tier of testing is performed with the UPS packaged inside its shipping carton including all associated packing materials. These tests include vibration, shock and drop testing. All test results are reviewed and if deemed acceptable, signed off by a DOT inspector. After receiving this approval all equipment shipments must be shipped at Class 9 Hazardous Materials and clearly identified as containing lithium batteries. Handling instructions must be placed on the outside of the shipping container along with the telephone number that can be contacted in case of an emergency. The staff of both the shipper and recipient shipping departments must be properly trained in the handling of hazardous materials and lithium batteries. The proper fire suppressant equipment must also be in place.
Lithium-Phosphate (LiFePO4) battery technology offers the UPS manufacturer the best hope. The technology appears to be one of the safest lithium battery chemistries due to its improved thermal and chemical stability. It is much more difficult to ignite a Lithium-phosphate battery in the event of mishandling. They have a better cycle life than other Lithium-ion chemistries and are more recyclable. Recycled phosphate can be used as fertilizer. Further, there is presently one manufacturer of Lithium-phosphate batteries that has designed their batteries with internal fusing, eliminating the need for BMS protection circuits. Due to this they have received a waiver from the DOT and can ship the batteries without a Class 9 hazardous materials declaration. However, only four 12 volt batteries may be connected in series without a BMS to provide equalization. Due to the characteristics of Lithium-Phosphate type batteries, the VRLA battery chargers found in some UPS designs can be used without modification.
At the present time, the costs, shipping and safety issues associated with the proper implementation of high-capacity Li-Ion batteries precludes their use in the majority of UPSs and only viable in vertical markets willing to pay the extra costs associated with Li-Ion batteries. Currently this consists of the military and a limited number of scientific markets. The Li-Ion battery’s high power density and associated reduction in battery pack size and weight are paramount to the higher costs associated with the UPS.
For more information, please visit Falcon Electric, Inc. at www.falconups.com.