Rich Byczek, Technical Lead for Electric Vehicle and Energy Storage, Intertek
People depend on batteries for a number of reasons. Pacemakers and defibrillators, for instance, work inside the body to keep the heart pumping. Mobile handset batteries power communication, facilitating a global marketplace and a fast-paced economy. Automobile batteries make it possible to travel at will. As these products and a host of others are being redeveloped and refined and consumers demand more from their devices, batteries have to be able to satisfy ever-increasing market demands.
Manufacturers in the Information Age have seen the marketplace and its dependence on bigger and better batteries change rapidly. This has altered the considerations for battery certification and consumers’ needs. Though consumers have always prioritized product safety, the wealth of information available allows them to be more knowledgeable than ever. Because of this, manufacturers will want to certify their products for additional safety standards that their competitors may not have, allowing them to make true marketing claims and boost their products’ appeal.
Another side effect of the past decade’s technological explosion is that the world’s connectedness has facilitated a global marketplace. The doors to international commerce have been flung open, expanding the market tenfold. Consequently, there are more competitors. This indicates that manufacturers should ensure their products satisfy international safety and performance standards along with domestic standards to stay competitive.
Lastly, the green movement has permeated the marketplace and consumers’ purchasing decisions. Manufacturers now prioritize green initiatives to soothe the collective consumer conscience. Backing up these claims with the proper certification will increase manufacturers’ credibility.
All of these factors are a major influence on the certifications manufacturers will need to achieve in the near future. Incorporating these factors into product development now will mitigate the costs of adaptation further down the line.
Safety First
Product safety is a crucial component of the development and manufacturing process. When batteries are recalled or worse, cause injury or death to a user, manufacturers will suffer financially. The damages manufacturers must pay in addition to the sunk costs of producing defective batteries will ultimately affect their bottom line.
Achieving safety certification for batteries is the legal requirement, but it is also the bare minimum. Although non-mandatory testing may appear to be wasteful, it often ensures a stronger product. Additionally, major retailers and end-product manufacturers oftentimes require additional certifications. Obtaining these certifications early in the manufacturing process is an effective way to help maintain relationships with major buyers. In essence, non-mandatory testing ensures product safety while solidifying important business relationships.
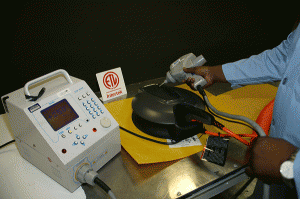
When submitting batteries for safety tests, manufacturers can expect that they will undergo procedures that examine how the batteries react in dangerous situations. A third party testing lab will be able to mimic the conditions batteries undergo and monitor their reaction. Many battery failures can be traced back to defects in the manufacturing process, specifically, foreign material within the battery that causes an internal short circuit. The more common attempted methods are to crush the battery or penetrate the battery with a metal rod. In addition, a recently proposed method requires the manufacturer to intentionally introduce the foreign material on a batch of batteries. This procedure simulates the manufacturing defect and shows that the design is robust enough that it will not cause a fire or other safety hazard, even if a manufacturing defect made it into the field.
Though battery life is a performance rather than a safety characteristic, safety certification requires battery life tests. The batteries will be aged either by short term storage at high temperatures or by continuously cycling the batteries though charge/discharge cycles. This cycling simulates potential failures that would never be seen with brand new batteries. The testing lab will be able to provide a report that shows the point where the error occurred.
With the knowledge gleaned from testing and observation, the testing lab can help manufacturers identify the most necessary points for improvement and collaborate on determining a solution. Early testing will also smooth out flaws in the beginning, decreasing the costs of redeveloping the product further down the road.
Due to the scope of devices that use batteries, there is no concrete definition of “good” battery life across the board. For instance, a cell phone battery only has to last until the next model comes out, whereas the performance standard in electric vehicles is a minimum of 10 years.
To Market, To Market —Transportation Certification
Transportation is unpredictable; there’s never a guarantee that cargo will arrive at the destination safely. When transporting hazardous materials, manufacturers and touch points through the supply chain take precautions to ensure the products arrive intact and without harming others on the road, airspace or other landscape.
While lithium batteries themselves are not hazardous material, they are high in energy density. Lithium batteries are small packages of extremely powerful energy, which means that they have the potential to react much more violently than other batteries. As a result, they can pose a hazard if handled incorrectly. This potential hazard necessitates certification before they can travel.
Since the safety and performance standards for batteries are not yet under an all-encompassing global certification, the United Nations maintains the guidelines for global transport. These guidelines protect denizens of all countries throughout the supply chain from harmful reactions. To meet these guidelines, batteries will undergo a series of tests that mimic the stresses they will endure throughout any given mode of transportation. If they go through the tests without reacting, they pass transportation certification. A lab will conduct the following tests on batteries seeking clearance for transport:
• Altitude Simulation
• Thermal Test
• Vibration
• Shock
• External Short Circuit
• Impact (Primary and Rechargeable Cells only)
• Overcharge (Rechargeable Batteries only)
• Forced Discharge (Primary and Rechargeable Cells only)
Addressing Environmental Concerns
Sustainability is a high priority for manufacturers. While lithium-ion (rechargeable) batteries are preferable to lithium (non-rechargeable) batteries for many manufacturers, considering the environmental effects of battery waste is both ethical and a cornerstone of battery certification.
Environmental certifications are important for a number of business reasons. As shown by the stricter EU Battery Directive, the global marketplace places high importance on sustainability. Certifying for global requirements will increase the battery’s competitiveness. Domestically, being “green” is considered an important part of being a good corporate citizen. Every day more companies are becoming conscious of their impact on the environment and taking great strides. Green certification boosts buyer appeal and allows device manufacturers to make green claims that support their products.
The current environmental safety standards for batteries are listed in the “Regulation on Batteries,” which is based off the EU Battery Directive. “Regulation on Batteries” has been slow to keep up with technologies and only covers certain toxic heavy metals. To satisfy all of the requirements in “Regulation on Batteries,” manufacturers must consider the following:
1. Chemical content
2. Battery lifespan and the number of cells required to achieve the desired battery function in the equipment or apparatus
3. Recyclability
The directive covers the limits by weight that a battery can contain of certain heavy metals, e.g., mercury, cadmium and lead. It also dictates how batteries should be collected and treated after their service life. Though these metals are covered in the directive, they do not play a role in the function or manufacturing of lithium batteries. Rather, they are the output of contaminated material and need to be monitored to avoid any potential harm.
Recycling is another key part of sustainability certification. Post-life, batteries can leak toxic chemicals. Manufacturers can expect to see stricter regulations on recycling batteries in the coming years due to the prioritization of governmental eco-initiatives.
Regulatory bodies currently do not have strict rules for battery recycling. As green initiatives become a higher priority, the government will likely impose stricter fines upon non-compliers and subsidize recycling procedures for those who do comply.
The Bottom Line
The overall certification challenge to manufacturers is the globalized economy, underlining the essentiality of conformity to domestic and global safety standards. To remain competitive in this marketplace, battery manufacturers will need to ensure their products can achieve these certifications. Being certified will drive sales from device manufacturers who need to choose batteries that will ensure their products are competitive. Forward-thinking product development is key to improving market share since proper certification requirements minimize the cost of restarting the product’s development. Additionally, a third-party testing lab can assist manufacturers with incorporating the standards into product development, ensuring a smoother testing and certification process.
For more information, please contact Intertek at www.intertek.com.
This article was printed in the January/February 2012 issue of Battery Power magazine.