Contributed Commentary by Maximilian Sackerer, Senior Business Consultant for Battery and Fuel Cell Manufacturing, Siemens AG
Powerful lithium-ion batteries are a key component both in electric vehicles and for the decentralized storage of electricity from renewable energy sources. Acceptance by car drivers depends on the capacity, safety, durability, and costs of the batteries and this, in turn, will determine the future of electric mobility. All these properties have to be brought up to a worldwide competitive level in the mass production of lithium-ion cells, and continuously improved.
The Center for Solar Energy and Hydrogen Research Baden-Württemberg (ZSW) in Ulm is been working on electrochemical energy storage since 1988. Since 2014 it has had “research platform for the industrial production of large lithium-ion cells”, or FPL for short. The facility is financed by the federal government and the state of Baden-Württemberg. It models a near mass production process for hard case battery cells. It comprises a number of distributed systems for the subsections: recipe preparation, electrode production, cell assembly, and formation. These have been deliberately designed as individual modular processes so that new solutions can be easily integrated and parts can also be used individually. The FPL is currently configured for the production of PHEV-1 cells (plug-in hybrid electric vehicle) with an assembly rate of around one cell per minute.
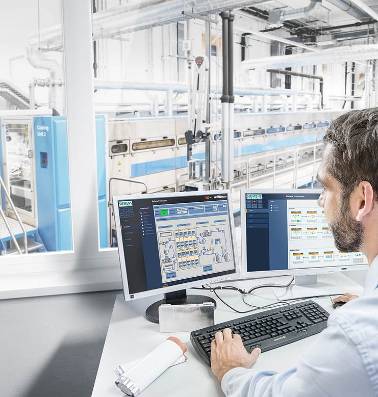
Research on Behalf of Industry
The researchers are focusing on investigating complex interactions of cell chemistry, cell design and, in particular, the production technology in respect of quality, safety, and manufacturing costs. They are also investigating inline sensor systems for production tolerances and cost-intensive processes. With new materials and components, the goal is to evaluate their usability and quality on an industrial scale. The core tasks of the researchers in Ulm is to optimize the production processes and to verify advanced cell chemistry in test series. This is being done within the scope of a research project for industrial customers, including a number of German automobile manufacturers. The ZSW team also ensures that the systems operate safely. It also supports its industrial partners with cost considerations and the implementation of new methods of quality assurance.
A SCADA System as the Common Element
The subprocesses are controlled, operated and monitored on the respective systems. In order to have everything under control at all times, all customer, order, material, recipe, process and quality data are pooled on a central control center (production control system). New experimental configurations are being developed “in the field”, then managed from the control center, and released for production. The heart of the control system is the SIMATIC WinCC SCADA system (version 7.x) from Siemens, which has proven itself in many industrial applications in diverse industries.
Together Toward the Solution
Working in close coordination with the ZSW team, the Siemens WinCC Competence Center in Stuttgart planned, configured, programmed, and implemented the control center. The supplier has many years of experience in the field of battery manufacture, and so could very quickly offer and implement a needs-based solution. The result is a distributed server-client system with two WinCC servers and several web clients in important plant sections. The latter have access to the servers via WinCC/WebNavigator and standard web browsers and offer the full range of functions, even locally.
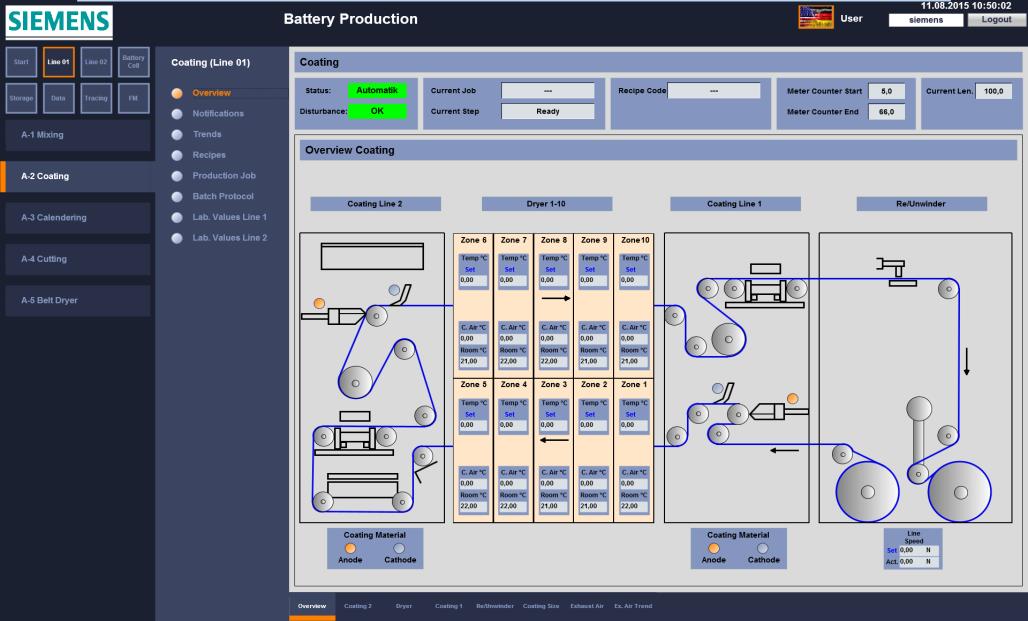
Simple, intuitive handling of the system was important to the operator, and this has been provided in the form of a flat menu structure with only four levels. So, with a few mouse clicks, the operator moves from the general overview to each plant section and the required information. For example, to trend curves of the coating thickness, which are based on “real-time” data of the inline measuring system, or to the alarm management.
This means that all processes can be monitored and analyzed online. In this way, parameter changes can be quickly recorded and every ongoing process can be readjusted when required. Data management across all processes enables factors influencing the entire value chain to be monitored by a single system, and included in the control chain. This leads to maximum process reliability and minimum deviations.
Another core task of the WinCC system is the central long-term archiving via SIMATIC Process Historian, a cross-product and cross-version real-time database for any volume of process data and any number of messages from various data sources. Any number of ad hoc reports and batch logs can also be created to enable a quick response in the event of a fault, or to compare parameter sets changed at runtime.
Open and Flexible Approach
Other than in the (large-scale) industrial environment, a research project is not about fully automated production of the largest possible quantities in the shortest cycle times. Dr. Wolfgang Braunwarth, head of production research (ECP), said, “On the contrary, in the future it will depend on having an open, flexible system, parts of which can also be used individually, and which can be relatively easily expanded to include further plants or components. With inflexible equipment, we cannot remain innovative for much longer, as research is currently being carried out in all directions all over the world.”
In addition to the integration of external measuring systems, simple access to laboratory data from the SCADA system was indispensable. The operator had also desired a connection to the product management/warehouse management system and to the building control system at ZSW. This enabled the effects of storage time and storage conditions of the sensitive materials on the quality of the cell to be investigated.
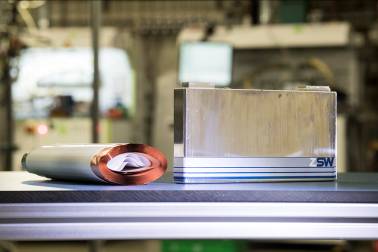
Production Research Depends on Data
The SCADA system pools this data, and records every change to the process parameters of all plant sections. Thus, for example, the coating thickness and calander press pressure and degree of dryness are all documented for every meter of electrode material, for each individual cell. From the external measuring system solutions anchored in the project, the most relevant measured values are recorded and correlated with other process parameters. For example, the around 30 individual values from the coating thickness measurements are reduced to three meaningful values, and passed on to the long-term archive of the SCADA system.
Stefan Rößler, who has accompanied the creation of the control center for ZSW, said, “Siemens has fulfilled all our requests, and implemented a very fine grained, user-friendly package management for modules and components. So, after the production of each cell, we know which materials have been used and how, as well as, for example, from which delivery batch the hard case cover came.”
This is also important if the cause of faults has to be determined in a subsequent field trial. Both in the control centers and for the web clients, anonymized customer, supplier and material component names ensure complete confidentiality. That is essential for sensitive research projects. For this reason, the operator deliberately forgoes all external interventions.
Safeguarded into the Future
Because ZSW cannot and will not maintain its control center itself, because it lacks the resources, it concluded a multi-year service and maintenance contract with Siemens. The spare part supply is also safeguarded for many years, and thus the availability of all plant sections equipped with Siemens components.
Blueprints for Commercial Manufacturing
The consistent use of standardized systems and components that have proven themselves in industry decisively simplifies and accelerates the know-how transfer. This enables solutions generated on the ZSW research platform to be used as blueprints for the (large-scale) industrial production of battery cells.