Commentary Contributed by Dr. John Duffy, Product Marketing Manager, Malvern Panalytical
October 20, 2017 | The multistep process used to manufacture battery electrodes must be closely controlled to produce components that deliver desirable electrochemical performance. In order to achieve this, the rheological properties of the slurries used during processing must be optimized, since these properties affect important characteristics such as slurry stability, ease of mixing, and coating performance, which impact on the properties of the finished electrode. Electrode slurries typically include electrochemically active materials, conductive additives, and binders, in addition to solvent, and both composition and the properties of each component can have an impact on the rheology of the resulting suspension. However, so too can the processing conditions applied. Each process step subjects a slurry to different stresses and each optimally calls for different rheological characteristics.
In this article, we look at the processes involved in the manufacture of electrodes for Li-ion batteries and the importance of rheology within this context. We introduce rotational rheometry as a valuable tool for characterizing battery slurries and highlight the measurements that can usefully be performed. Example data from an experimental study of the impact of processing parameters on electrode performance illustrates the relevance of rheological characterization in the development and manufacture of high performance electrodes.
Manufacturing Battery Electrodes
The key steps involved in the manufacture of cathodes and anodes for Li-ion batteries are shown in Figure 1. The raw materials typically include the active material, some form of conductive additive such as carbon (e.g. carbon black and/or graphite), and a polymeric binder dissolved in a solvent. The active material and carbon are both introduced in the form of dry powders which may or may not be premixed ahead of slurry formation. The role of the binder is to hold the active particulate material together and in contact with the metal substrate in the finished electrode. A commonly used binder is polyvinylidene fluoride (PVDF) which is traditionally dissolved in N-methylpyrrolidone (NMP). However, the expense, toxicity and flammability of NMP make replacement a current target for the industry, with water-based binders such as styrene butadiene rubber (SBR) an attractive alternative.
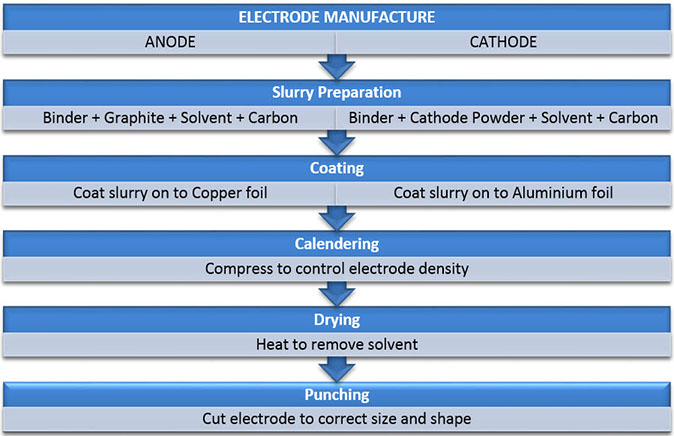
The slurry is prepared by mixing the particulate material and binder together to form a uniform slurry/suspension, which is then applied to a copper (or other conductive metal) foil in a continuous coating process. The solvent is then driven off to produce a dried coating which is subjected to calendaring, a compression process that involves feeding the coated foil through a series of rollers. Finally, the finished electrodes are punched or cut to size ahead of incorporation in the battery.
The structure of the electrode coating directly impacts the electrochemical performance of the battery and can be controlled through choice of constituent components, compositional adjustment, and by manipulating the physical properties of the raw materials such as particle size distribution or particle shape. Processing conditions also exert a significant influence on electrode structure. For example, the extent to which raw materials are dispersed during the slurry manufacturing process affect the size of particles deposited on the foil, while the size of compressive forces applied during calendaring directly influences the porosity of the finished coating.
These are not discrete effects, rather changes made during one step can have an impact on consecutive processes, as well as the properties of the finished electrode. For instance, dispersion of the raw materials to a finer particle size may influence the rheology of the slurry, which impacts on the coating process and then the calendaring process. This network of process-structure (fα ,fβ and fγ) and process-process (fa, fb and fc) interactions and the resulting process-structure-property relationships (YPSP and YPSP+) are represented in Figure 2.[1]
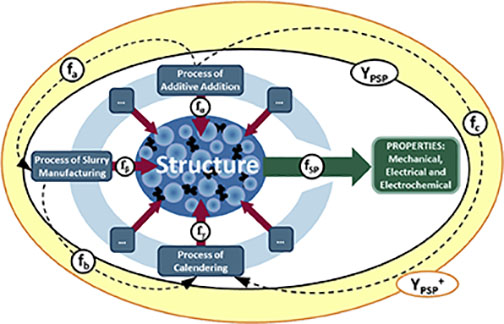
Focusing on Rheology
Rheological measurements quantify the ease with which materials flow. They characterize the degree of structure within the sample and the extent to which liquid- or solid-like behavior dominates. In the electrode manufacturing process, the rheology, particularly the viscosity, of the in-process materials is relevant at a number of points, for example:
- The viscosity of the polymeric binder solution influences the ease with which powders are dispersed within it and the power required for mixing;
- The rheological properties of the slurry affect its stability, whether particles remain uniformly suspended within it, or are prone to settling, thereby compromising homogeneity;
- The rheology of the slurry also influences coating performance, the speed with which a uniform coating can be applied, layer thickness on the foil and edge profile.[2]
The rheology of a solution or suspension can be controlled in numerous ways. For example, the viscosity of the polymeric binder solution can be manipulated by changing the concentration of polymer within the solution, or by varying properties of the polymer such as molecular weight/molecular weight distribution.[3] The rheological properties of the slurry, on the other hand, are a function of the[4]:
- particle size and particle size distribution of the raw powders;
- particle shape and particle shape distribution of the raw products;
- solids loading within the slurry;
- the viscosity of the continuous phase.
These variables also impact other aspects of the process and the performance of the finished electrode so there are constraints on the extent to which they can be varied to control rheology. Optimizing the rheological properties of the in-process streams within these constraints is an important but challenging goal that relies in the first instance on the measurement of relevant rheological metrics.
Introducing Rotational Rheometry
When it comes to choosing a system to carry out the rheological studies needed to support electrode manufacture, it is helpful to carefully consider measurement requirements. Viscosity is an important property at most points in the process so a primary requirement is a system that can generate relevant viscosity data for all process streams.
Most industrially-encountered fluids, including those involved in electrode manufacturing processes, are complex (two-phase) and non-Newtonian. This means that the viscosity they exhibit is dependent on the shear rate to which they are subjected, the rate at which shear force is applied. Non-Newtonian behavior can be extremely useful. For example, engineering an electrode slurry to have structure at low shear will enhance its stability and edge profile control during coating2, while lower viscosity at high shear will aid raw material dispersion. However, in terms of the practicalities of rheological characterization, it means that viscosity must be measured under conditions that are representative of those applied in the process to be robustly relevant.
Viscometers are widely used across industry for viscosity measurement but often measure at just a single shear rate or over a fairly limited range, compromising their value for process optimization studies. A rotational rheometer, in contrast, enables measurement across a very broad range of shear rates, thereby enabling far more complete characterization.
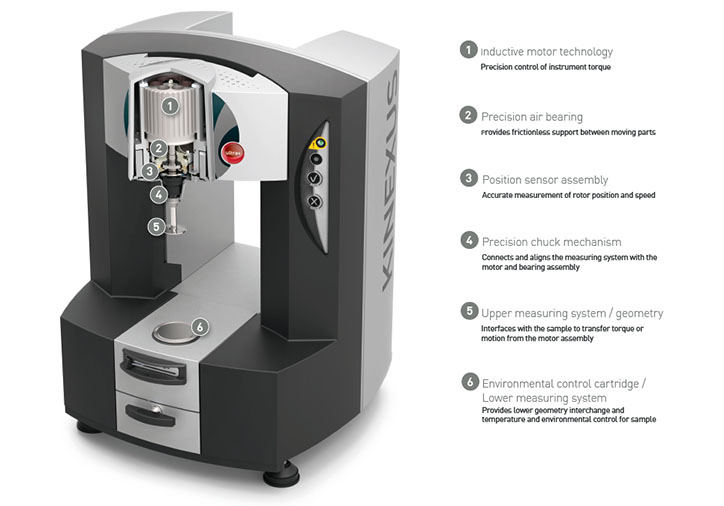
Figure 3 shows a cutaway image of a rotational rheometer highlighting the key components of the system including inductive motor, air bearing, position sensors, and measuring systems. As shown in Figure 4 the sample is loaded between the upper and lower measuring systems, which in the illustrated example are parallel plates, and subjected to a rotational shear stress (σ). This is driven by a torque from the motor, which causes the top plate to rotate relative to the stationary lower plate. The resulting strain rate (shear rate) is then determined from the rotational speed of the upper plate, measured using position sensors, and the height of the shearing gap.
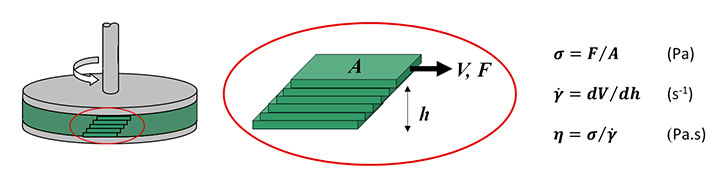
The accuracy and range of shear rates and shear stress that can be applied with a modern rotational rheometer allows the testing of materials ranging from very low viscosity, weakly-structured fluids, through to stiff pastes and gels, comfortably spanning the sample types encountered in electrode manufacturing. Furthermore, test types extend well beyond the generation of simple viscosity flow curves (plots of viscosity against shear) to oscillatory methods for the detailed investigation of sample structure. These can be particularly useful for polymer solution studies, to optimize binder solution properties, for example, in the development of water-based processes with comparable performance to NMP analogues. Rotational rheometers can therefore comfortably provide the level of rheological support required for optimizing battery slurries and are widely used in such applications, as the following case study illustrates.
Investigating the impact on slurry rheology of composition and processing conditions
Researchers at the Institute for Particle Technology,TU Braunschweig, Germany have conducted a multi-parameter study into the how slurry rheology is affected by composition and the processing conditions applied during slurry manufacture. The results form part of a much broader study into the effects of processing on the structural and electrochemical properties of Li-ion batteries.1 In this study, composite cathode electrodes were prepared in accordance with the recipes and processing matrix shown in Table 1 and Figure 5 respectively.
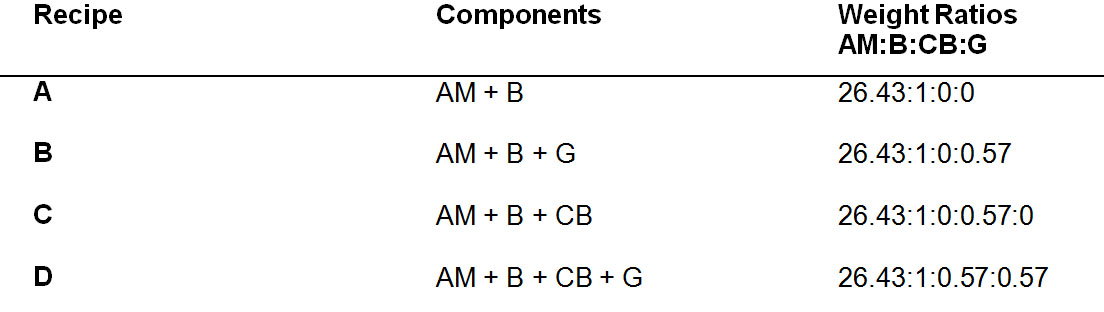
- AM is Active material (Li(Ni1/3Co1/3Mn1/3)O2 (NCM; HED NCM-111, BASF SE))
- CB is carbon black (C-NERGY SUPER C65,Timcal Ltd.)
- G is graphite (C-NERGY KS6L, Timcal Ltd.)
- B is binder (polyvinylidene fluoride Solef 5130, Solvay Solexis)
- NMP is N-Methyl-2-pyrrolidone (standard grade, BASF SE)
In terms of composition, the recipes vary with respect to the conductive additive used, either carbon black or graphite. Recipe A contains neither, while Recipe D contains both. Recipe B contains graphite alone, while Recipe C contains carbon black alone. Beyond these differences in composition, back-to-back trials were carried out with Recipes C and D using two different manufacturing processes: reference and intensive. The first step of the process, in both cases, was to dissolve the binder in NMP for 30 minutes and degas the resulting solution.
For the intensive process, the next step involved dry mixing for four minutes in a high intensity shear mixing device (Nobilta, Hosokawa Alpine AG). The equivalent step in the reference process was carried out in a 3Dmotion mixer (Turbula, Willy A. Bachofen AG Maschinenfabrik), with mixing applied for 15 minutes to blend the active material with carbon black and a further five minutes to enable graphite incorporation. In all cases, the resulting powder mixtures were dispersed for 60 minutes in the NMP-binder mixture using a dissolver (Dispermat CA, VMA Getzmann) and the solids content was standardized.
The resulting suspensions were used to prepare electrodes via the processing steps indicated in Figure 5, but were also subject to rheological characterization using a rotational rheometer (Kinexus pro+, Malvern Panalytical). Equilibrium flow curves were generated using a cone and plate geometry (4o, 40 mm) at a temperature of 20o°C. Measurements were carried out by logarithmically increasing shear rate, with a temperature equilibration time of 2 minutes between each measurement.
Full details of the complete experimental study can be found in Reference 1.
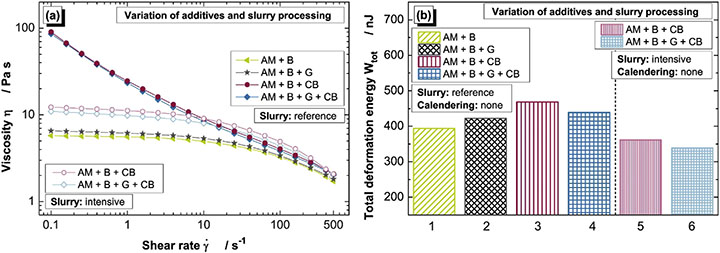
All the slurries produced exhibit shear thinning behavior, with a pronounced reduction in viscosity at high shear rates. However, at low shear rates (<10s-1), two markedly different types of behavior can be observed. Comparing just the slurries subjected to the reference process, those that do not contain carbon black exhibit a plateau with a very slight gradient, indicating that they retain liquid-like behavior at low shear. In these suspensions, the AM particles can slide optimally, relative to one another, and viscosity is largely a function of the properties of the continuous phase, the binder and solvent. The shear-thinning behavior observed at higher shear rates is attributable to orientation and stretching of the binder molecules.
In contrast, the slurries containing carbon black exhibit a yield point. These suspensions show a significant viscosity increase at low shear rates that is indicative of more solid-like behavior and significant structure within the slurry due to carbon agglomeration. As a result, they are likely to be more stable, presenting greater resistance to sedimentation. Slurries containing carbon black that are subjected to the intensive preparation do not exhibit a yield point, but rather show behavior closely similar to the graphite only recipes. The intensive deagglomeration of the carbon black clearly has a marked effect on how it impacts slurry rheology.
These observed differences also correspond with electrode compressibility and hence calendaring performance, as shown in Figure 6b. Wtot represents total deformation energy, measured using nano-indentation test, with smaller values indicating stiffer structures, which are more difficult to compress. The samples with highly agglomerated carbon black additives (reference process), which show yield stress behavior (bars no. 5 and 6), compress more readily than those with dispersed carbon black additives (intensive process), which show a viscosity plateau at low shear rates.
These results indicate that while all the slurries exhibit the shear-thinning behavior that is advantageous for electrode slurry performance, the parameters of the coating process need to be carefully manipulated in each case to ensure their optimal handling and processing. The broad conclusion from the study is that the choice of conductive additive, addition method and the calendaring process applied all influence the mechanical and electrochemical properties of the resulting electrode. Rheological characterization helps to elucidate how changes to, for example, the slurry recipe, go on to influence the coating conditions that must be applied and, consequently, the performance of the finished product.
In Conclusion
Controlling the mechanical and electrochemical properties of electrodes is essential to access high levels of battery performance. Understanding and manipulating the rheology of the slurries used in electrode manufacture is important within this context, since rheology directly impacts in-process performance. Optimally tuning processing parameters to slurry rheology enhances process efficiency, but the conditions applied during mixing, additive addition and calendaring also have a direct impact on the properties of the finished electrode. Rotational rheometry can help electrode manufacturers to generate data to solve the complex optimization challenge that this creates and produce electrodes that deliver the very highest levels of performance.
References
[1] Bockholt, H et al ‘The interaction of consecutive process steps in the manufacture of lithium-ion battery electrodes with regard to structural and electrochemical properties’ Journal of Power Sources 325 (2016) 140-151
[2] Bitsch,B et al ‘A novel slurry concept for the fabrication of lithium-ion battery electrodes with beneficial properties’ Journal of Power Sources 265 (2014) 81 – 90
[3] Malvern Panalytical. Measuring the rheology of polymer solutions. Malvern white paper available for download at:
https://www.malvern.com/en/support/resource-center/Whitepapers/WP150324MeasRheologyPolymerSols.html
[4] Malvern Panalytical. Exploring the impact of particle characteristics on suspension rheology. Available at: https://www.malvern.com/en/support/resource-center/Whitepapers/WP170213ParticlePropertiesSuspensionRheology.html