Isidor Buchmann, CEO and Founder
Cadex Electronics, Inc.
Batteries work well when new and confidence falls after the first packs fade and need replacing. In time, the battery fleet becomes a jumble of good and bad batteries, and that’s when the headache begins.
Batteries exhibit human-like qualities. They need good nutrition, prefer cool temperature, but suffer from abuse. Care begins by operating them at cool temperatures, using moderate charge rates and going easy on discharge. It is better not to run batteries down too low but to charging them more often. Avoid ultra-fast charging and harsh loading conditions. There is some truth to why well-cared batteries outperform neglected ones; studies can back this up.
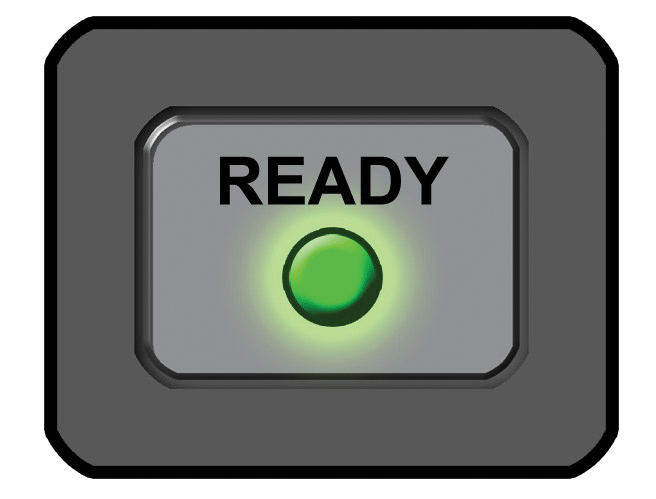
The Ready light indicates that the battery is fully charged. This does not mean “able.” There is no link between “ready” and battery performance.
Battery charging is generally well understood, but the “ready” light is misconstrued. Ready does not mean “able.” There is no link to battery performance, nor does the green light promise a full runtime. Batteries always charge completely, even the weak ones, and ready simply means that the battery is full. With age, the ability to hold charge shrinks and the charge time shortens. This causes faded batteries to gravitate to the top, disguised as combat ready. System collapse is imminent when workers scramble for freshly charged batteries in an emergency. Those glowing ready may be deadwood. (The charge time of a partially charged battery is also short.)
The amount of energy a battery can hold is measured in capacity. Capacity is the leading health indicator that determines runtime and predicts end-of-battery-life. A new battery is rated at 100 percent, but few packs in service deliver the full amount. A workable capacity bandwidth is 80 to 100 percent. As a simple guideline, a battery on a portable device having a capacity of 100 percent typically provides a runtime of ten hours, 80 percent is eight hours and 70 percent seven hours.
The service life of a battery is specified in number of cycles. Lithium- and nickel-based batteries deliver between 300 and 500 full discharge/charge cycles before the capacity drops below 80 percent. Cycling is not the only cause of capacity loss; keeping a battery at elevated temperature also induces stress. A fully charged Li-Ion kept at 40°C (104°F) loses about 35 percent of its capacity in a year without even being used. Ultra-fast chargers and punitive discharging is also harmful, causing a cut in battery life to half, and hobbyists can attest to this.
Battery Maintenance
Batteries are commonly serviced on a battery analyzer. These instruments became popular in the 1980s to restore nickel-cadmium batteries affected by “memory.” With memory absent in Li-Ion, the purpose of a modern battery analyzer is to keep fleet batteries at an acceptable performance level and to retire them when low. Device manufacturers endorse battery analyzers, knowing that well-performing packs reflect positively on their devices, a win-win situation for both parties.
Conventional battery analyzers measure capacity by discharging a fully charged battery and tracking the elapsed time. This procedure is time-consuming and stresses the battery. Rapid-testing is preferred but this only provides estimated state-of-health values and the degree of accuracies varies with the method used. Public safety, medical and defense organizations still rely on periodic full discharge/charge cycles.
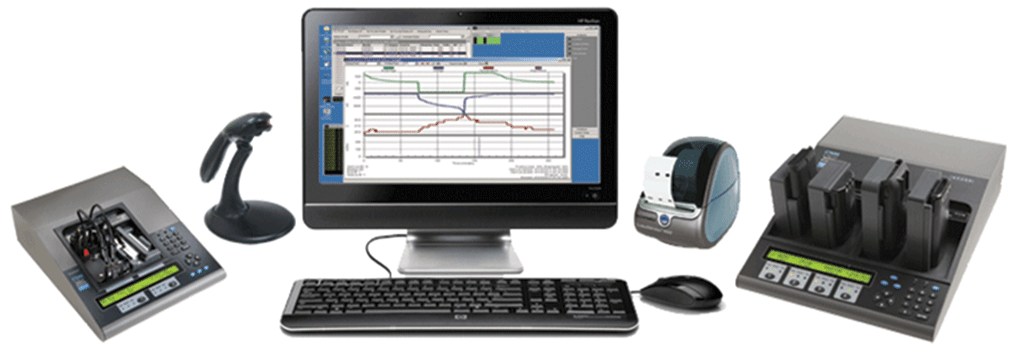
With PC software, the computer becomes the command center.
Most battery analyzers feature multi-bays to service a diverse group of batteries. Custom battery adapters configure the analyzer to the correct setting and smart cables enable programming on the fly. With PC software, the computer becomes the host from which all functions are entered. Clicking the mouse on a battery listed in the database configures the analyzer to the correct setting. The user can add, remove and edit the batteries. Figure 2 illustrates Cadex battery analyzers running on PC-BatteryShop displaying battery test results in real time.
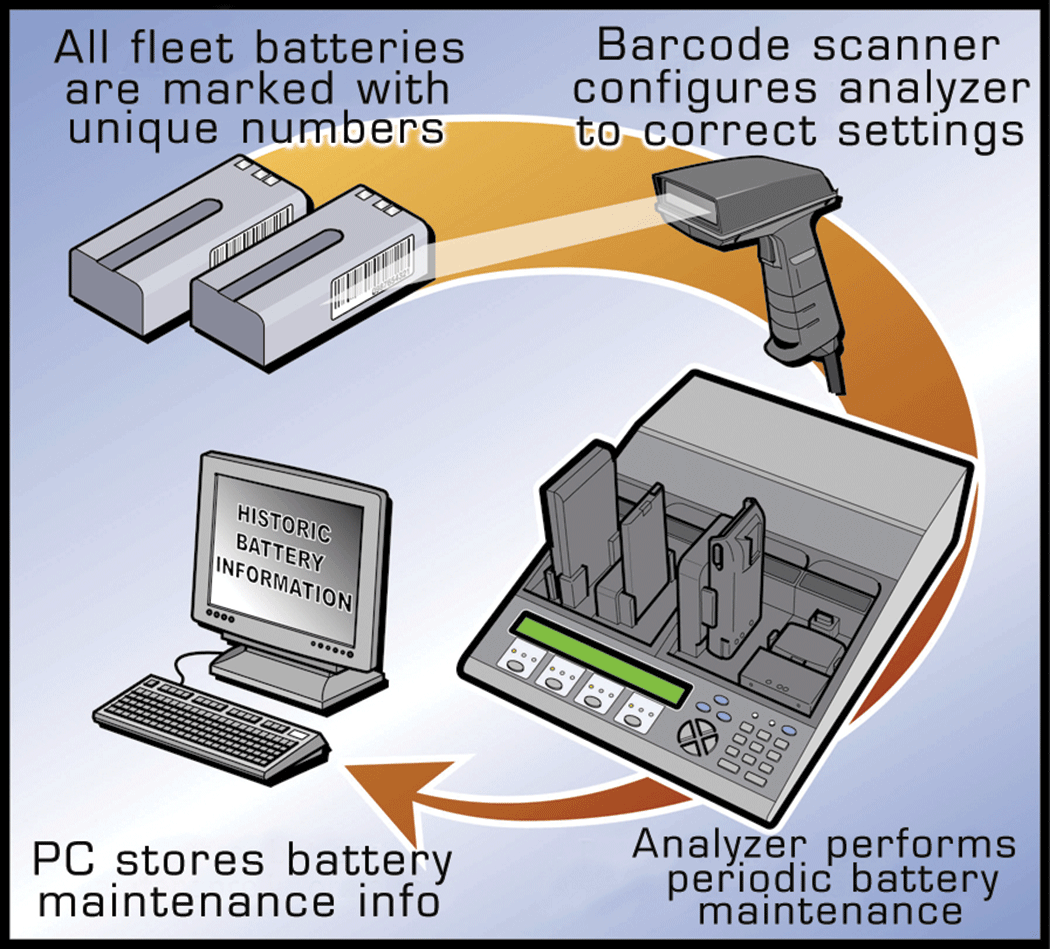
Labeling each battery with a unique ID number simplifies battery service. Swiping the barcode label prepares the analyzer for service. Past logs are displayed on the monitor.
PC-operated battery maintenance systems offer several services, one of which is marking all batteries with a permanent ID number. A printer generates these labels in bar code format. To service a battery, the user simply scans the label and inserts the battery into the analyzer. Past battery performance data are made available that may also include purchasing dates, vendor information and pricing. Figure 3 illustrates such a system.
Another service method is attaching a label that displays the last service, due date, capacity and internal resistance. Figure 4 illustrates such a label. The system is self-governing in that a prudent user will only pick a battery that has been serviced and meets the capacity requirements. Expired packs are analyzed and if the capacity requirements are met, relabeled and returned to service.
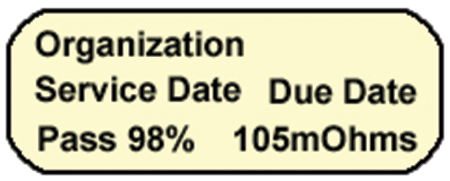
Battery Label
Basic battery data and service
information are contained on a label.
Most fleet operations use 80 percent as a battery pass/fail criterion. A day’s work is not complete without also examining the reserve capacity before recharge, and a battery analyzer can perform such spot checks. If the lowest-performing battery in the fleet still has 20 to 30 percent reserve, then the target capacity can be lowered to 70 percent. Such fine-tuning finds the sweet spot between risk management and economics.
Battery analyzers also perform incoming inspections. A new vendor may offer a lower-priced pack but the performance, consistency and longevity are unknown. The analyzer automatically cycles the battery and stops at selected target capacity, storing the cycle count, voltage and temperature characteristics.
Rechargeable batteries do not die suddenly but the capacity diminishes gradually. Batteries in daily use should be serviced once every one to three months. The time required is minimal; analyzing a battery fleet with an automated battery analyzer requires only about 30 minutes per day. A four-station battery analyzer offers a throughput of about 160 batteries when done on a monthly maintenance schedule.
In-house battery maintenance is not practical for everyone and large organizations hire outside firms to provide this service. The incoming battery specialist will first validate all batteries by a full analysis and replace packs that do not meet the capacity threshold. Good batteries are identified with a service label and returned. Test intervals and capacity threshold will need to be agreed prior. A two-tier system may be installed in which lower-capacity batteries are reassigned to less critical applications. Such a maintenance procedure leads to higher reliability and lower operating costs.
Batteries in Warehouse Logistics
Many IT Managers are faced with the daunting task of keeping battery replacement costs down and system reliability high. Some device manufacturers recommend replacing the battery annually, but such advice only suits the battery supplier as the cost and environmental impact would be prohibitively high. Batteries have improved, so has the service life. In addition, some applications are energy savvy and batteries with capacities as low as 70 percent can power the scanner for an entire shift. There is no need to replace these batteries too soon, but the state-of-health of the fleet batteries must be known.
An IT manager of a warehouse logistics facility in the US said this about their newly installed battery management system (paraphrased).
“Experiencing continuous high battery replacement costs, we purchased a battery maintenance system. After only four months of use, we saved over $6,800 using the Cadex C7400. Next year we hope to save over $10,000. The ability to analyze our battery inventory has not only reduced our yearly cost on new batteries but also lowered downtime for employees. Batteries last for the full shift; defective batteries are identified and removed immediately.”
Battery maintenance eliminates battery-related breakdowns and saves money. The payback of a modern battery analyzer is typically less than one year; improved reliability and environmental benefit are side benefits. Operation is simple and the required service time per day is short.
Isidor Buchmann is the founder and CEO of Cadex Electronics Inc. For three decades, Buchmann has studied the behavior of rechargeable batteries in practical, everyday applications, has written award-winning articles including the best-selling book “Batteries in a Portable World,” now in its third edition. Cadex specializes in the design and manufacturing of battery chargers, analyzers and monitoring devices.
For more information visit www.batteryuniversity.com and www.cadex.com.